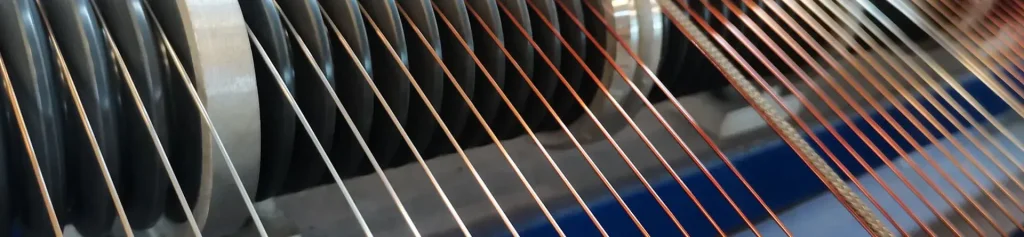
5 Points Difference of Performance of Copper VS Aluminum
Connectivity
Oxides, chlorides, or sulfides of the base metal are much more conductive for copper than aluminum. This fact makes cleaning and protecting the joints for aluminum connections more important. Some consider copper-to-aluminum connections incompatible. Also questionable are the transition connections between aluminum transformers and copper building wire.
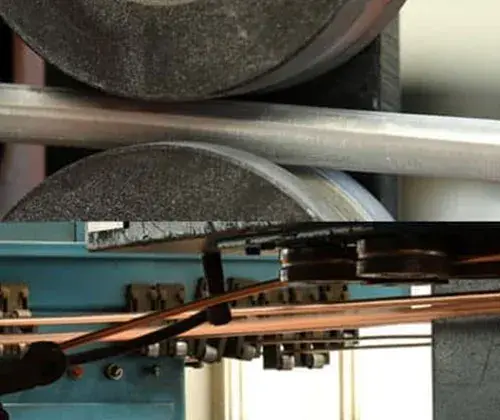
Coefficient of Expansion
Aluminum expands nearly one third more than copper under changing temperatures. This expansion, along with the ductile nature of aluminum, has caused some problems when bolted connections are improperly installed. To avoid joint loosening, some type of spring pressure connection is necessary. Using either cupped or split washers provides the necessary elasticity at the joint without compressing the aluminum. By using proper hardware, aluminum joints can be equal in quality to copper joints.
Thermal Conductivity
Some argue that the thermal conductivity of copper is superior to that of aluminum in reducing hot-spot temperature rise in transformer windings. This is true only when copper and aluminum windings of identical wire size, geometry, and design are compared. Therefore, for any given transformer kVA size, the thermal conductivity characteristics of aluminum can be very close to those of copper. For aluminum coils to achieve the same current-carrying capacity as copper, the aluminum coil must be approximately 66% larger in its cross-sectional area. Responsible manufacturers design and test the hot-spot characteristics of their designs and utilize cooling surface area, coil geometry, air ducting, and conductor shape to produce acceptable hot-spot gradients regardless of winding material.
Electrical Conductivity
Often, arguments point to the inferiority of aluminum conductivity, citing the fact that aluminum has only 61% of the conductivity of copper, which causes higher energy losses in aluminum transformers. Designers are always concerned with winding temperature. To keep the temperature below the insulation rating, aluminum transformers are designed with aluminum conductors of larger cross-sectional area than copper. On average, this results in energy losses that are the same for aluminum as for copper. Therefore, transformers of similar design with the same temperature rise have roughly equivalent losses regardless of conductor material.
Tensile Strength
The lower tensile and yield strength of aluminum has prompted some concern about its use in cyclic load applications. Loads drawing high peaks of current such as DC drives and other SCR controllers, create electromagnetic forces that can cause movement of conductors and coil leads. As shown in Table 2, aluminum has only 38% of the tensile strength of copper. However, the table comparison is based on equal cross-sectional area. As previously noted, to obtain equal ratings in aluminum transformers, it typically requires 66% more cross-sectional area than copper conductors. The use of larger-sized conductors results in aluminum winding strength nearly equivalent to copper windings. The ability of a transformer to withstand the long-term mechanical effects of “high impact” loads depends more on adequate coil balance and lead support than on conductor choice. No significant difference in mechanical failure has been experienced between copper or aluminum low voltage transformers.
Connectivity
Connectivity is by far the most common reason for “prejudice” against the use of aluminum-wound transformers. Both copper and aluminum are prone to oxidation or other chemical changes when exposed to the atmosphere. The problem is that aluminum oxide is a very good insulator, whereas copper oxide, although not considered to be a good conductor, is not nearly as troublesome in bolted connections. Cleaning and brushing with a quality joint compound to prevent oxidation is recommended for either material and simply more essential for aluminum.