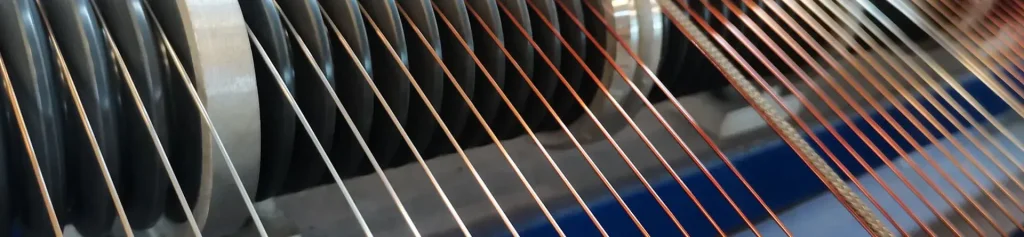
Polyester Or Polyesterimide Overcoated With Polyamide-Imide Enamelled Round Aluminium Wire, Class 200
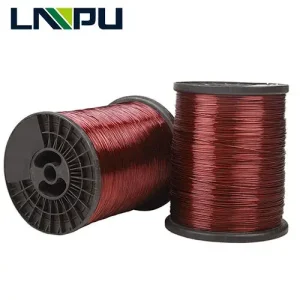
Enamelled round aluminium wire with coatings of polyester or polyesterimide, and over coated with polyamide-imide. Its represents a specialized type of magnet wire used in various high-performance electrical and electronic applications. This combination of materials ensures excellent thermal, mechanical, and electrical properties, making it suitable for demanding environments.
The combination of polyester or polyesterimide with polyamide-imide coatings on aluminium wire provides more high-performance, cost-effective. Its enhanced thermal stability, mechanical durability, and chemical resistance make it ideal for transformers, motors, generators, coils, and other demanding applications.
Base Material: Aluminium. Lightweight and flexible. Excellent electrical conductivity. Cost-effective compared to copper.
Primary Coating: Polyester or Polyesterimide.
This is extensively used wire enamel with excellent thermal properties, class 180 or above. It can be applied to single-coating and double-coating applications.
Adequate thermal stability:These coatings can typically withstand temperatures up to 180°C, making them suitable for high-temperature applications.
Provides good insulation and mechanical strength. Resistant to solvents and chemicals.
Secondary Coating: Polyamide-Imide.
Polyamide-imide (PAI) is known for its superior thermal and chemical resistance. Excellent mechanical-property retention at elevated temperatures.
PAI can endure temperatures up to 220°C or higher, extending the wire’s operational range. It offers exceptional resistance to a wide range of chemicals, including solvents and corrosive agents.
Winding wire temperature
Class 200 is a thermal class that requires a minimum temperature index of 200 and a heat shock temperature of at least 220℃.
The temperature in degrees celsius corresponding to the temperature index is not necessarily. It is recommended that the wire be operated and this will depend on many factors, including the type of equipment involved.
Cut-through: No failure shall occur within 2 min at 320℃.
Temperature index:Clause 15 of lEC 60317-0-3:2008 and lEC 60317-0-3:2008/AMD1:2013 applies. The minimum temperature index shall be 200.
Resistance to refrigerants:The percentage of extractable matter shall not exceed 0,5%. The requirement for breakdown voltage shall be 75% of the minimum specified value.
Specifications – IEC 60317-25-2020 Standard
Reference standard the requirements for Polyester or polyesterimide over coated with polyamide-imide enamelled round aluminium wire, class 200.
This part of lEC 60317 specifies the requirements of enamelled round aluminium winding wires of class 200 with a dual coating. The underlying coating is based on polyester or polyesterimide resin. It can be modified provided it retains the chemical identity ofthe original resin and meets all specified wire requirements. The superimposed coating is based on polyamide-imide resin.
This wire features a primary coating of polyester or polyesterimide. And a secondary overcoat of polyamide-imide. It designed to provide enhanced thermal, mechanical, and electrical properties.
The range of nominal conductor diameters covered by this document is:
Grade 0,250 mm up to and including 3,150 mm;
Grade 0,250 mm up to and including 5,000 mm.
The nominal conductor diameters are specified in Clause 4 of lEC 60317-0-3:2008 and IEC 60317-0-3:2008/AMD1:2013.
Resistance to abrasion (nominal conductor diameters up to and including 2,500 mm)
The wire shall meet the requirements given in Table 1.
For intermediate nominal conductor diameters,the value of the next largest nominal conductor diameter shall be taken.
Table 1 – Resistance to abrasion | ||||
Nominal conductor diametermm | Grade 1 | Grade 2 | ||
Minimum average force to failureN | Minimum force to failure of each measurement N | Minimum average force to failureN | Minimum force to failure of each measurement N | |
0,400 0,450 0,500 0,560 0,630 0,710 0,800 0,900 1,000 1,120 1,250 1,400 1,600 1,800 2,000 2,240 2,500 |
1,95 2,10 2,25 2,40 2,55 2,75 2,95 3,15 3,40 3,70 3.95 4,25 4,60 5,00 5,30 5,70 6,10 |
1,65 1,75 1,90 2,05 2,20 2,35 2,50 2,70 2,90 3,10 3,35 3,60 3,90 4,20 4,50 4,80 5,15 |
3,15 3,40 3,60 3,85 4,15 4,45 4,75 5,10 5,45 5,80 6,25 6,65 7,15 7,70 8,20 8,75 9,30 |
2,65 2,85 3,05 3,25 3,50 3,75 4,05 4,30 4,60 4,90 5,25 5,45 5,85 6,50 6,95 7,40 7,90 |
Advantages and Benefits
Cost-Effective: Aluminium offers a more economical alternative to copper, reducing overall production costs. Aluminium offers a more affordable alternative to copper without compromising performance.
Thermal Stability:The combination of polyester, polyesterimide, and polyamide-imide coatings provides excellent thermal stability. The wire to perform reliably at elevated temperatures. This makes it suitable for applications where heat generation is significant, such as in motors and transformers. Capable of withstanding high operating temperatures. Retains insulation properties under thermal stress.
Electrical Insulation Properties:High dielectric strength ensuring that the wire can handle high voltages without breakdown. This is crucial in preventing short circuits and maintaining the efficiency of electrical systems.
Mechanical Durability:The mechanical strength of these coatings protects the wire from physical damage during handling, installation, and operation. This includes resistance to abrasion, impacts, and bending stresses. Otherwise it will affect the performance of the wire.
Chemical Resistance:The chemical resistance of polyester, polyesterimide, and polyamide-imide ensures that the wire remains unaffected by exposure to solvents, oils, and other corrosive substances. This enhances the wire’s longevity and reliability in harsh environments.
In summary, polyester or polyesterimide overcoated with polyamide-imide enamelled round aluminium wire offers a compelling combination of cost-effectiveness, performance, and durability. Among the various types of enamelled wires, those made of aluminium and coated with polyester or polyesterimide, and polyamide-imide stand out due to their unique properties and advantages.
The combination of polyester/polyesterimide with polyamide-imide provides a versatile solution that meets multiple performance criteria effectively. Class 200 enamelled wires are suitable for high-temperature applications, ensuring reliability and durability. Superior thermal stability, mechanical durability, and chemical resistance make them ideal for demanding environments.