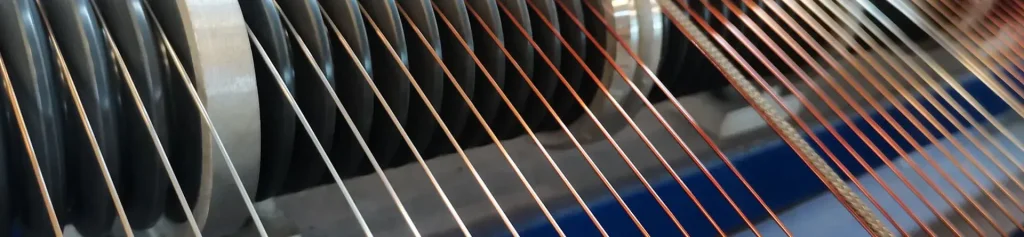
Aluminium Foil For Transformer Winding
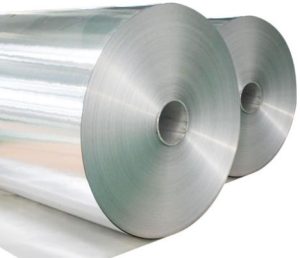
Introduction
Aluminium foil for transformer winding have very high conductivity and thermal conductivity, their conductivity is up to about 60%IACS, and forming, welding and corrosion resistance are very good, so it can well meet the performance requirements of aluminum foil for transformer.
Transformer aluminium foil can be used for variable transformer like low or high voltage transformer winding, high frequency transformer,step up or down voltage transformer etc. The alloy can be used to meet the minimum industry requirements for strip conductor, is closely controlled to assure smooth, substantially burr-free edges and strip-size avail-abilities are in capacities exactly equivalent to those of standard copper wire sizes.
In dry type transformers, aluminum winding have been commonly used. Aluminum strip can replace copper conductor in distribution transformers.
Product Description of aluminum foil for transformer winding
Product name | 1050 1060 1070 1350 O Aluminium foil for Transformer winding |
Grades | 1050 1060 1070 1350 |
Temper | O |
Specification | Thickness:0.2-3.5mm Width:20-1350mm |
Quantity tolerance | ±10% |
ID | 152.4,200,300,400 and 500mm |
Surface treatment | Mill finish |
Application | Transformer winding |
Packaging | Wooden Pallet |
Payment terms | TT,30% deposit and 70% balance before shipment,LC at sight |
Delivery time | 10 days |
MOQ | 1 Tons |
Port | Shanghai port, Qingdao Port |
Sample | The sample of Aluminium foil strip is available. |
Remark | 1050 1060 1070 1350 Aluminium foil strip can be customized. |
Chemical Composition of aluminium foil for transformer
1050 Aluminium foil strip Chemical composition(%) | |||||||||
Element | Al | Si | Fe | Mg | Zn | Mn | Ti | Cu | V |
Standard Value | ≥99.5 | 0.0431 | 0.203 | 0.0013 | 0.0093 | 0.0104 | 0.0200 | 0.0022 | 0.0039 |
1060 Aluminium foil strip Chemical composition(%) | |||||||||
Element | Al | Si | Fe | Mg | Zn | Mn | Ti | Cu | V |
Standard Value | ≥99.6 | 0.0431 | 0.203 | 0.0013 | 0.0093 | 0.0104 | 0.0200 | 0.0022 | 0.0039 |
1070 Aluminium foil strip Chemical composition(%) | |||||||||
Element | Al | Si | Fe | Mg | Zn | Mn | Ti | Cu | V |
Standard Value | ≥99.7 | 0.0431 | 0.203 | 0.0013 | 0.0093 | 0.0104 | 0.0200 | 0.0022 | 0.0039 |
1350 Aluminium foil strip Chemical composition(%) | |||||||||
Element | Al | Si | Fe | Mg | Zn | Mn | Ti | Cu | V |
Standard Value | ≥99.5 | 0.0431 | 0.203 | 0.0013 | 0.0093 | 0.0104 | 0.0200 | 0.0022 | 0.0039 |
Advantages
For example, the principal advantage to using aluminum foil rather than copper in transformers is the reduction in weight. The density of copper is .32117 lbs. per cubic inch while that of aluminum is .09765 lbs. per cubic inch. For a given winding volume, the aluminum winding would weigh one-third the weight of the copper. However, aluminum has only 60% the conductivity of copper. If the winding volume is increased by 40% to raise the aluminum conductivity to that of copper, it still leaves the aluminum coil weighing only 42% of the equivalent copper coil.
Applications
Power Transformers
Distribution Transformers
Dry-Type Transformers
Low-Frequency Transformers
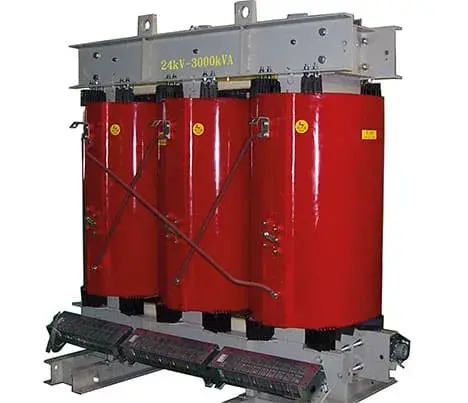
Considerations
Lower Conductivity Compared to Copper: To achieve the same electrical resistance, aluminum conductors need to have a larger cross-sectional area than copper conductors, which might require more space.
Mechanical Strength: Aluminum is not as strong as copper, which can make it more prone to mechanical damage during winding and handling.
Thermal Expansion: Aluminum has a higher coefficient of thermal expansion compared to copper, which can cause mechanical stresses in the windings during temperature changes.
Connector and Joint Issues: Special care is needed when connecting aluminum to other materials to avoid galvanic corrosion and ensure reliable electrical connections. Typically, aluminum requires crimped or bolted connections rather than soldered ones.
Techniques for Using Aluminum Foil in Transformer Windings
Layer Winding: Aluminum foil is wound in layers, separated by insulation, to create a compact and efficient winding structure. This technique is particularly effective in reducing eddy current losses.
Interleaved Winding: In some designs, aluminum foil is interleaved with insulating materials to improve voltage distribution and reduce dielectric stress.
Automated Winding Machines: Specialized winding machines are often used to precisely wind aluminum foil, ensuring consistent tension and alignment, which is crucial for performance and reliability.
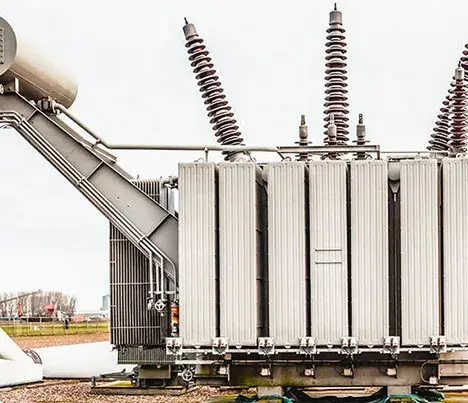
How to make the aluminum foils?
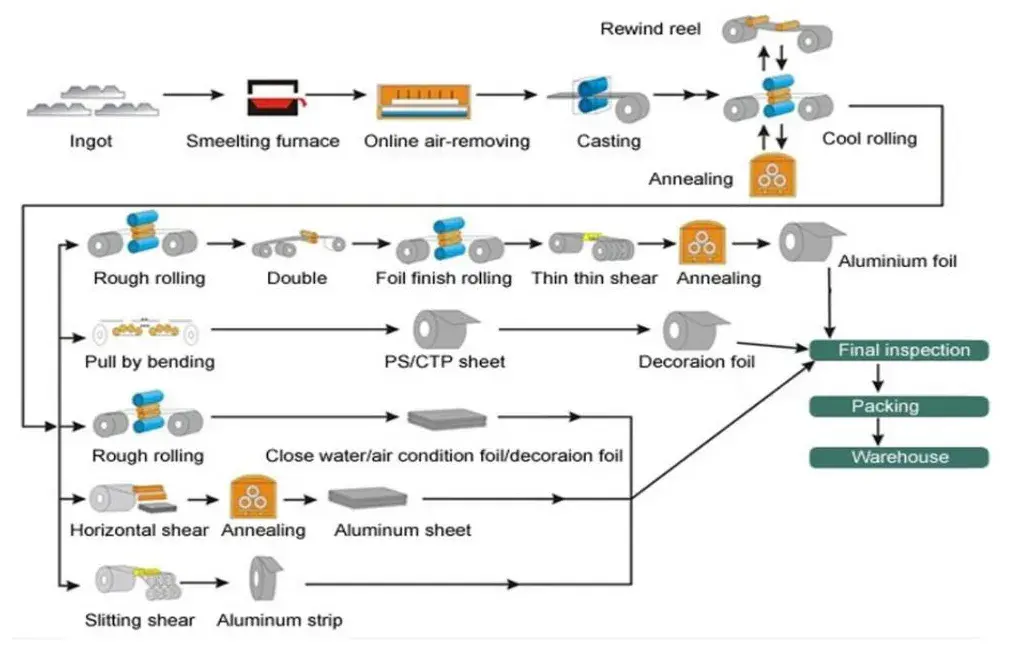