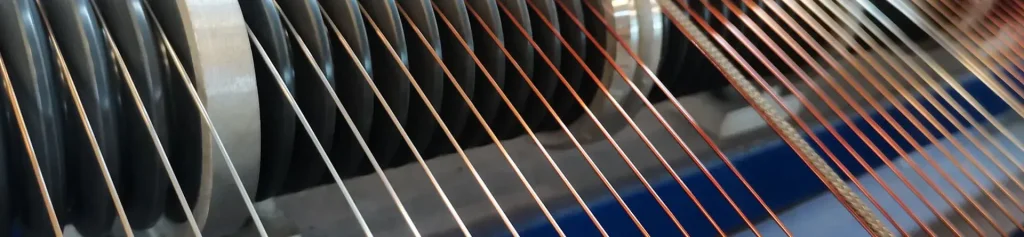
Class 120 PolyvinyI Acetal Enamelled Round Copper Wire
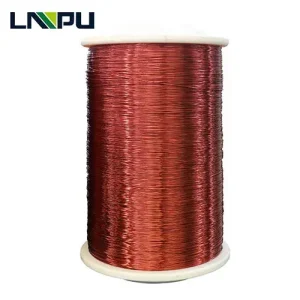
Polyvinyl acetal enamelled copper wire is a type of insulated wire where the conductor is coated with a layer of polyvinyl acetal enamel. This enamel serves as an insulating material, protecting the copper conductor from environmental factors and electrical stresses. The “Class 120” designation refers to the thermal endurance of the wire, indicating that it can operate reliably at temperatures up to 120°C.
Polyvinyl acetal enamelled round copper wire, classified under Class 120, is a crucial material in the field of electrical engineering. This type of wire is renowned for its excellent insulation properties, durability, and ability to withstand high temperatures.
Specifications – IEC 60317
Reference standard lEC 60317 the requirements of enamelled round copper winding wires class 120 with a sole coating based on polyvinyl acetal or polyvinyl formal resin. It can be modified provided it retains the chemical identity of the original resin and meets all specified wire requirements.
NOTE 1 A modified resin is a resin that has undergone a chemical change, or contains one or more additives toenhance certain performance or application characteristics.
NOTE 2 Polyvinyl acetal is a general name for a family of thermoplastic vinyl resins produced by thecondensation of polyvinyl alcohol with an aldehyde.Examples are polyvinyl acetal, polyvinyl formal and polyvinylbutyral.
The range of nominal conductor diameters covered by this document is:
Grade 1: 0,040 mm up to and including 2,500 mm;
Grade 2: 0,040 mm up to and including 5,000 mm;
Grade 3: 0,080 mm up to and including 5,000 mm.
Temperature and qualified standards
Class 120 is a thermal class that requires a minimum temperature index of 120 and a heatshock temperature of at least 155°C. The temperature in degrees Celsius corresponding to the temperature index is not necessarilythat at which it is recommended that the wire be operated and this will depend on manyfactors, including the type of equipment involved.
1. Cut-through test:No failure shall occur within 2 min at 170°℃; Resistance to abrasion (nominal conductor diameters from 0,250 mm up to and including 2,500 mm).
2. Flexibility and adherence:Clause 8 of lEC 60317-0-1:2013 applies,where the constant K used for the calculation of thenumber of revolutions for the peel test shall be 175 mm.
3. Heat shock: Clause 9 of lEC 60317-0-1:2013 applies. The minimum heat shock temperature shall be155°℃.
4. Nominal conductor diameters up to and including 1,600 mm.
The coating shall show no crack. The mandrel diameter shall be as specified in Table 1.
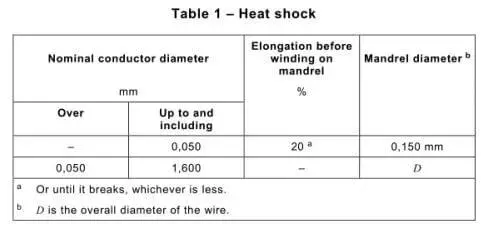
5. Resistance to abrasion (nominal conductor diameters from 0,250 mm up to and including 2,500 mm)
The wire shall meet the requirements given in Table 2.
For intermediate nominal conductor diameters, the value of the next larger nominal conductordiameter shall be taken.
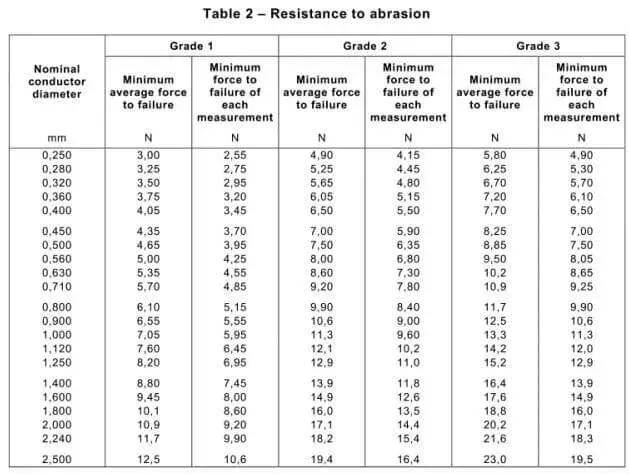
Characteristics & Advantages
1. Low Electrical Resistance: The copper conductor in these wires has low electrical resistance, ensuring efficient conductivity and minimal energy loss. This property is vital for applications where high efficiency is required.
2. Dielectric Strength: The polyvinyl acetal enamel provides excellent dielectric strength, allowing the wire to withstand high voltages without electrical breakdown. This makes the wire suitable for use in high-voltage applications.
3. Tensile Strength: The wire exhibits high tensile strength, making it resistant to breaking or stretching during installation and operation. This durability is essential for applications involving mechanical stress.
4. Flexibility: Despite its strength, the wire remains flexible, which facilitates easy winding and installation in various electrical devices.
5. Thermal Endurance: As a Class 120 wire, it can withstand continuous operation at temperatures up to 120°C. This thermal stability is crucial for applications exposed to high operating temperatures.
6. Thermal Conductivity: The copper conductor provides excellent thermal conductivity, which helps in dissipating heat generated during electrical operation.
7. Moisture Resistance: The polyvinyl acetal enamel provides effective resistance against moisture, preventing corrosion and degradation of the copper conductor.
8. Chemical Resistance: The enamel also protects the wire from various chemicals, ensuring long-term durability and reliability even in harsh environments.
Considerations
While polyvinyl acetal enamelled round copper wire offers numerous benefits, there are considerations to keep in mind:
1. Handling and Installation. Care must be taken during handling and installation to avoid damaging the enamel coating. Scratches or abrasions can compromise the insulation properties, leading to potential electrical failures.
2. Temperature Limits. Although the wire can withstand temperatures up to 120°C, operating beyond this limit can degrade the enamel coating and reduce the wire’s lifespan. Proper thermal management is essential to maintain the wire’s performance.
3. Compatibility. Ensuring compatibility with other materials and components in electrical devices is crucial. The wire’s chemical resistance must be matched with other elements to avoid adverse reactions that could affect performance.
Polyvinyl acetal enamelled round copper wire, Class 120, is an essential component in modern electrical and electronic applications. Its excellent electrical, mechanical, and thermal properties make it suitable for a wide range of uses, from electrical motors and transformers to consumer electronics and automotive components. By understanding its characteristics, advantages, and potential challenges, professionals in the industry can effectively utilize this wire to enhance the performance, efficiency, and reliability of their electrical systems. If you are interested in this Polyvinyl acetal enamelled wire, please contact us!