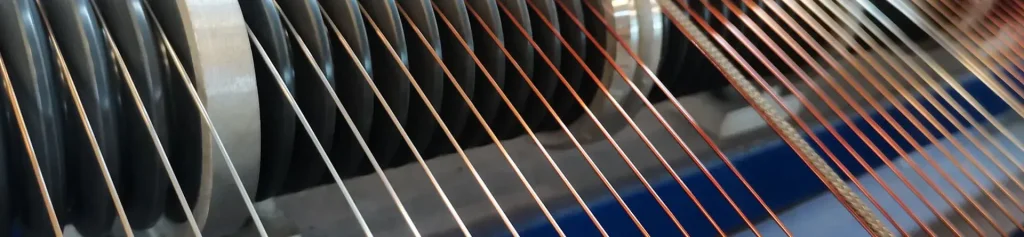
Enameled Round Aluminum Wire
- Winding
- Even and Tight Winding: Care must be taken to wind the wire evenly and tightly to avoid gaps and ensure consistent performance.
- Tension Control: Maintain appropriate tension during winding to prevent breaking the wire.
- Connections
- Stripping Insulation: Carefully strip the enamel coating from the ends where connections are made.
- Special Connectors: Use connectors designed for aluminum to ensure reliable electrical and mechanical connections.
- Anti-Oxidation Measures: Apply anti-oxidation compounds at connection points to prevent corrosion.
- Mechanical Handling
- Avoid Kinks and Bends: Handle the wire carefully to avoid kinks and sharp bends that can damage the enamel coating and the wire itself.
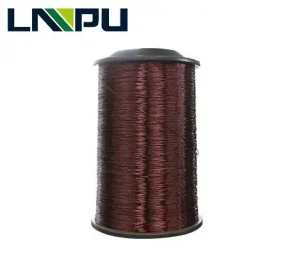
Enameled round aluminum wire is a type of magnet wire that consists of an aluminum conductor coated with a thin layer of enamel insulation.
Enameled Round Aluminum Wire structure
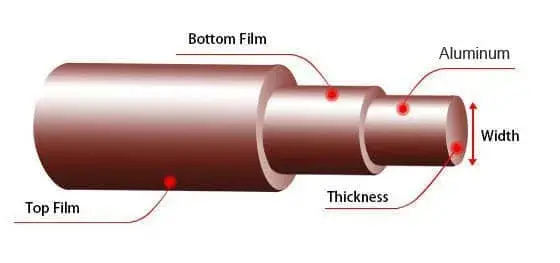
Diameter of our transformer enameled round aluminum wire
Name | Enameled Round Aluminum Wire |
Conductor | Aluminum |
Dimension | Diameter: 0.16-9.2mm |
Thermal Class | 120(Class E), 180(Class H), 200(Class C), 220(Class C+), 240(Class HC) |
Insulation Thickness: | G1; G2 or single build; heavy build |
Standard | IEC 60317-16,60317-16/28,MW36 60317-29 BS6811, MW18 60317-18 ,MW20 60317-47 |
Certificate | UL |
Packing | 30kg-150kg ply-wood spool(250*400 / 250*500/ 250*600/ 250*730) |
Insulation Building:Single & Heavy/double coated
The insulating materials are subdivided according to IEC standards into insulating classes showing the corresponding maximum working temperature that must not be exceeded at any point of the winding.
The table above outlines the recognized insulation classifications.
INSULATION CLASSIFICATIONS ACCORDING TO IEC | ||
Class | Temperature | |
°C | °F | |
E | 120 | 248 |
B | 130 | 266 |
F | 155 | 311 |
H | 180 | 356 |
C | 200 | 392 |
C+ | 220 | 428 |
Features
Excellent bending property
High flexibility of the enamel
Good resistance to abrasion
High mechanical property
Higher thermal property
Good resistance to refrigerant and freon
Suitable for windings that are subjected to constantly high temperature and mechanical stress
Good chemical resistance
Outstanding mechanical and chemical property
Standards and insulation materials of enameled round aluminum wire
Thermal Class | Insulation types | NEMA Standard(MW1000) | IEC Standard | Federal Specification(JW1177) |
105℃ | Plain Enamel | NONE | NONE | NONE |
Formvar | MW 15 (RD) MW 18 (SQ & RECT) | 60317-1(RD) 60317-17(SQ & RECT) | JW 1177/ 14 (RD) JW1177/ 16 (SQ & RECT) | |
Formvar Bondable | MW19 | 60317-5 | JW 1177/6 | |
130℃ | Polyurethane Nylon Bondable – 130 | NONE | NONE | NONE |
155℃ | Polyurethane – 155 | MW79 | 60317-20 | JW1177/ 41 |
Polyurethane Nylon – 155 | MW80 | 60317-21 | JW1177/42 | |
Polyurethane Bondable – 155 Polyurethane Nylon Bondable – 155 |
MW131 MW 136 |
60317-35 NONE |
NONE NONE |
|
Dacron Glass – 155 | MW 45 (RD) MW 46 (SQ & RECT) | NONE(RD) 60317-60(SQ & RECT) | JW 1177/ 20 (RD)JW1177/ 25 (SQ & RECT) | |
180℃ | Polyurethane – 180 | MW82 | 60317-51 | NONE |
Polyurethane Nylon – 180 | MW83 | 60317-55 | NONE | |
Polyester-imide | MW30 | 60317-8 | JW 1177/ 12 | |
Polyester-Nylon | MW76 | 60317-22 | JW 1177/38 | |
Solderable Polyester | MW77 | 60317-23 | JW 1177/39 | |
Solderable Polyester Nylon | MW78 | NONE | JW 1177/ 40 | |
Polyurethane Bondable – 180 Polyurethane Nylon Bondable – 180 |
MW132 MW137 |
NONE NONE |
NONE NONE |
|
Polyurethane Nylon Bondable – 180 | MW137 | NONE | NONE | |
Polyester-imide Bondable Polyester-amide-imide Bondable Solderable Polyester Bondable |
NONE 60317-37 NONE |
MW 102 60317-38 NONE |
NONE 60317-36 NONE |
|
Dacron Glass High Temp | MW 51 (RD) MW 53 (SQ & RECT) | NONE(RD) 60317-61(SQ & RECT) | JW 1177/ 32 (RD)JW1177/ 34 (SQ & RECT) | |
200℃ | Polyester – 200 | MW74 | 60317-42 | JW 1177/43 |
Polyester A/I Topcoat | MW 35 (RD) MW 36 (SQ & RECT) | 60317-13(RD) 60317-29(SQ & RECT) | JW 1177/ 14 (RD)JW1177/ 13 (SQ & RECT) | |
Polyester A/I Polyamideimide | MW73 | 60317-13 | NONE | |
240℃ | Polyimide – ML | MW 16 (RD) MW 20 (SQ & RECT) | 60317- 46(RD) 60317- 47(SQ & RECT) | JW 1177115 (RD)JW1177/ 18 (SQ & RECT) |
Application
Transformers: especially used for distribution system power transformers where cost and weight savings are important.
Electric Motors: employed in motor windings, especially in applications where the reduced weight of aluminum can enhance performance.
Inductors and Coils: uses in inductors and various types of coils for electronic circuits.
Generators: utilized in generator windings to convert mechanical energy into electrical energy.
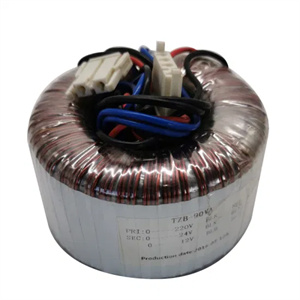


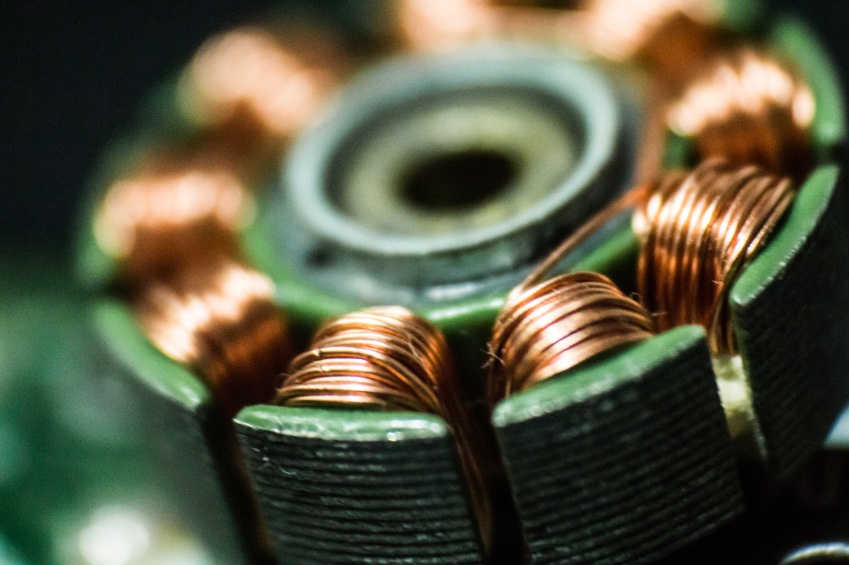
Advantages
Cost-Effective: Lower material cost compared to copper.
Lightweight: Easier to handle and install, reducing the overall weight of the finished product.
Good Thermal Performance: The enamel coating provides good heat resistance.