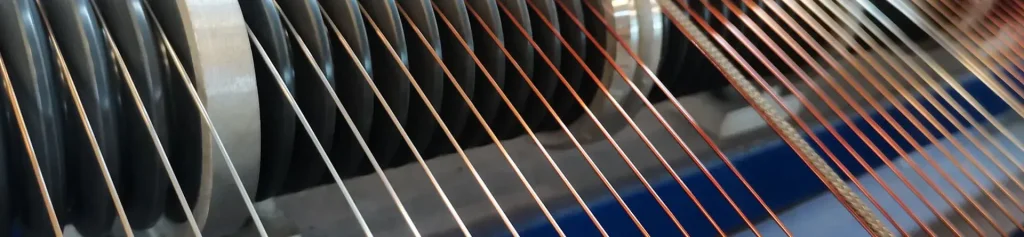
Glass Fiber Wrapped Enameled Flat Copper Wire 180
- Elongation
- Copper flat wire processing: high-purity copper materials are made into flat wires through stretching, rolling and other processing procedures.
- Insulation paint coating: special molds or equipment are used to evenly coat the high-temperature resistant insulation paint on the surface of the copper flat wire.
- Glass wire wrapping: after the insulation paint is cured, glass wire is used for wrapping to form a glass wire wrapping layer.
- Finished product inspection: the finished product is tested for electrical properties, heat resistance, mechanical strength and other aspects to ensure that it meets quality requirements.
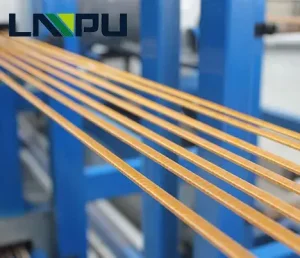
Overview
Glass Fiber Wrapped Enameled Flat Copper Wire 180 is a high-performance wire material designed for applications that require high temperature resistance, high voltage and high current. It combines the excellent insulation of glass fiber and the stability of enameled wire, as well as the good heat dissipation of flat copper wire, so that the wire can maintain excellent electrical performance under extreme conditions. In particular, its 180-level heat resistance ensures that the wire can also work stably in high temperature environments.
Material Properties
High temperature resistance: The 180-level heat resistance enables it to maintain stable electrical performance in high temperature environments without softening or melting.
Excellent insulation: The glass fiber wrapping layer provides excellent insulation performance for the wire, effectively preventing current leakage and electrical failure.
High electrical performance: The copper core conductor ensures the low resistance and high conductivity of the wire, making current transmission more efficient.
Mechanical properties: The glass fiber wrapping layer enhances the mechanical strength of the product and improves wear resistance and tensile resistance.
Good heat dissipation: The flat copper wire design increases the heat dissipation area of the wire and effectively reduces the temperature of the wire during operation.
Dimensions
3.1 Conductor size
– Width from 2.00mm to 16.00mm (inclusive);
– Thickness from 0.80mm to 5.6mm+ (inclusive).
The width/thickness ratio should be greater than or equal to 1.4:1, but not more than 8:1
width | Thickness | ||||||||||||||||||
0,80 | 0,90 | 1,00 | 1,12 | 1,25 | 1,40 | 1.60 | 1,80 | 2.00 | 2,24 | 2,50 | 2,80 | 3,15 | 3,55 | 4,00 | 4,50 | 5,00 | 5,60 | ||
Corner radius (0,5 mm*) | Corner radius (0.5 mm*) | Corner radius (0.65 mm*) | Corner radius (0,80 mm) | Corner radius(1,0 mm*) | |||||||||||||||
2,00 | 1,463 | 1,626 | 1,785 | 2,025 | 2,285 | 2,585 | |||||||||||||
2,24 | 1,655 | 1,842 | 2,205 | 2,294 | 2,582 | 2,921 | 3,369 | ||||||||||||
2,50 | 2,076 | 2,285 | 3,785 | 4,137 | Not recommendedRatio width/thickness smaller than 1,4:1 | ||||||||||||||
2,80 | 2.103 | 2.585 | 2,921 | 3,285 | 3,705 | 4,265 | 4,677 | 5,237 | |||||||||||
3,15 | 2,383 | 2,661 | 2,935 | 3,313 | 3,723 | 4,195 | 5,307 | 5,937 | 6,693 | ||||||||||
3,55 | 2,703 | 3,021 | 4.223 | 4,755 | 6,027 | 6,737 | 7,589 | 8.326 | |||||||||||
4,00 | 3,063 | 3,426 | 3,785 | 4,265 | 4,785 | 5,385 | 6,185 | 6,831 | 7,637 | 8,597 | 9,451 | 10,65 | |||||||
4,50 | 3,463 | 3,876 | 4,285 | 4,825 | 5,410 | 6,085 | 6,85 | 7,737 | 8,631 | 9,717 | 10,70 | 12,05 | 13,63 | ||||||
5,00 | 3,863 | 4,326 | 4,785 | 5,385 | 6,035 | 6,785 | 7,785 | 8,637 | 9,637 | 10,84 | 12,18 | 13,45 | 15,20 | 17,20 | |||||
5,60 | 4,363 | 5,385 | 6,057 | 6,785 | 7.625 | 8,745 | 9,717 | 10,84 | 12.18 | 13,45 | 15.13 | 17,09 | 19.33 | 21,54 | |||||
6,30 | 4,903 | 13,75 | 15,20 | 17,09 | 19,30 | 27,49 | |||||||||||||
7,10 | 6,216 | 6,885 | 7,737 | 9,725 | 11.15 | 12,42 | 15.54 | 17.20 | 19.33 | 24,66 | 27.54 | 31,09 | 34.64 | ||||||
8,00 | 7,785 | 8,745 | 9,785 | 10,99 | 12,59 | 14,04 | 15,64 | 17,56 | 19,45 | 21,85 | 24,65 | 27,85 | 31,14 | 35,14 | 39,14 | 43,94 | |||
9,00 | 9,865 | 11,04 | 12,39 | 14,19 | 15,84 | 17,64 | 19,80 | 21,95 | 24,65 | 27,80 | 31,40 | 35,14 | 39,64 | 44,14 | 49,54 | ||||
10,0 | 12.29 | 13,79 | 15.79 | 17.64 | 19,64 | 22,04 | 24,45 | 27,45 | 30.95 | 34.95 | 39.14 | 44,14 | 49,14 | 55.14 | |||||
11,2 | 15,47 | 17.71 | 19,80 | 22,04 | 24,79 | 27,46 | 30,81 | 34,73 | 39,21 | 43,94 | 49,54 | 55,14 | 61,86 | ||||||
12.5 | 19.79 | 22.14 | 24,64 | 27,64 | 30.70 | 34,45 | 43.83 | 49.14 | 55,39 | 61,64 | 69,14 | ||||||||
14,0 | Ratio width/thickness over 8:1 | 24,84 | 27,64 | 31.00 | 38,65 | 43,55 | 49.15 | 55,14 | 69,14 | 77,54 | |||||||||
16,0 | 31.64 | 35,48 | 39.45 | 44,25 | 49.85 | 56.25 | 63.14 | 71,14 | 79,14 | 88,74 | |||||||||
Nominal thicknessNOTE Dimensions according to R 20 series are printed in larger type |
-1 level GL1: One layer of glass fiber covering layer (GL1) on the 1 level enameled conductor (1 level)
Two layers of glass fiber covering layer (GL2) on the 1 level enameled conductor (1 level)-2 level GL1:
One layer of glass fiber covering layer (GL1) on the 2 level enameled conductor (2 level)-2 level GL2:
Two layers of glass fiber covering layer (GL2) on the 2 level enameled conductor (2 level)
Insulating paint
Polyurethane paint: has good water resistance, weather resistance and chemical resistance, suitable for various harsh environments.
Polyesterimide paint: has good heat resistance and insulation performance, can meet the electrical requirements in high temperature environment.
Size increase caused by insulation and bonding layer
4.1 Enameled wire without bonding layer
The increase in width or thickness caused by insulation shall comply with the provisions of Table 2.
Table 2-Increasesin dimensions
Grade | Increase in dimensions mm | ||
Minimum | Nominal | Maximum | |
12 | 0,060,12 | 0,0850,145 | 0,110,17 |
4.2 Enameled wire with bonding layer
For grades 1B and 2B, the dimensional increase due to the bonding layer shall be (0,04 ± 0,01) mm.
The elongation after rupture shall be measured in accordance with clause 20 of ISO 6892-1:2016. When the nominal strength, plastic elongation is not specified or the nominal strength, plastic elongation is required to be 80 N/mm², the limits in Table 3 apply.
Table 3-Percentage elongation after fracture
Nominal thickness of the conductormm | Minimum elongation% | |
Over | Up to and including | |
2,505,60 | 2,505,6010,00 | 303235 |
When values of nominal yield strength and plastic elongation are specified, the measured yield strength shall be within the tolerance range given in Table 4.
Table 4-Proof strength and resistivity
Proof strength | MaximumresistivityQ-mm² ·m-1 | |
Nominal valueN ·mm-2 | Tolerance | |
80120150180 | -0/+30 % -0/+20 % -0/+20 % -0/+20 % | 1/581/581/581/57,5 |
Production process:
Application areas
New energy vehicles: used in high temperature and high pressure environments such as battery management systems and drive systems.
Motor manufacturing: used to manufacture various types of motors, such as generators, motors, etc., to meet their high requirements for electrical transmission.
Transformer manufacturing: used as winding wires in transformers to ensure the stability and safety of current transmission.
Electrical equipment: used as electrical connecting wires and winding wires in various electrical equipment to improve the performance and reliability of the equipment.
Summary
Glass fiber wrapped enameled rectangular copper wire 180 grade has broad application prospects in the electrical field. With the rapid development of the power industry, new energy and electric vehicles, we will continue to optimize the production process and improve product quality to meet the changing market.