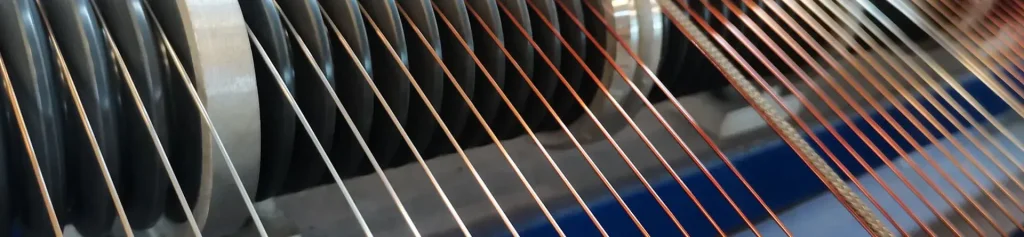
4 Type Of Self-Bonding Enameled Wire And Application
Acetal resin: Early self-adhesive paint base components used polyvinyl butyral (PVB) resin and polyvinyl formal resin. The most widely used field of PVF resin is the electrical insulation of magnet wires. It can be used as baseline insulation (high-strength acetal enameled wire, refrigerant-resistant enameled wire, etc.), and can also be used as a self-adhesive layer of composite wires. PVF modified with phenolic aldehyde has self-adhesive properties when coated on poly-cooled enameled wire. PVB resin as a self-adhesive layer can cover most common enameled wires. Solderable polyurethane enameled wire, covered with PVB resin to make it self-adhesive and solderable at the same time. This kind of thermoplastic self-adhesive wire is mainly used for small non-skeleton coils and is a traditional shaped product. It is worth noting that the same PVB self-adhesive paint is coated on different polyurethane base lines, and its direct solderability is different. Due to the different content of -NOO groups in the polyurethane paint film (different resin components) and the influence of the overcoating process, the direct solderability of this self-adhesive wire may be lost. When a suitable accelerator is added, the self-adhesive direct welding performance of the enameled wire is significantly improved. In order to improve the mechanical strength of the self-adhesive enameled wire and improve its comprehensive performance, there are also self-adhesive wires of polyurethane/nylon/butyral system abroad, that is, a nylon coating is added between the base line and the self-adhesive layer. Thermoplastic acetal resin composite enameled wire generally has a low temperature resistance grade (A~E grade), but the presence of -OH groups in the acetal resin molecule can make the acetal not only crosslink itself but also with some thermosetting resins (phenolic, Isocyanate, etc.) for cross-linking and curing, thereby increasing its use temperature. The self-adhesive layer of the self-adhesive wire is made of isocyanate modified PVB resin (also contains phenolic and tacky polyester resin), and can be selectively maintained in a thermoplastic state or turned into a thermoset through a controllable curing step as needed. status. After this self-adhesive enameled wire is bonded, it still maintains good bonding strength at less than 15C. It is widely used in the manufacture of winding wires for fractional horsepower motors including sealed motors (refrigerant resistant) and ordinary motors.
Epoxy resin: Generally, the heat resistance of epoxy resin is higher than that of acetal resin. Epoxy-based self-adhesive paints have better diluting properties and better coating processability. The corresponding self-adhesive thread can be used in Class B occasions. According to the patent, the self-adhesive thread made by mixing vinegar epoxy resin and nylon copolymer prepared by the reaction of bisphenol A with epichlorohydrin and dibasic acid has better performance than butyral self-adhesive thread. Especially it has good water and humidity resistance. The amine-modified epoxy self-adhesive layer (including crosslinking agent) can be melt-bonded at 125°C and can be further cured into an infusible thermosetting state. Compared with fusible bonding, infusible bonding has greater high-temperature bonding strength after bonding. The adhesive layer can be a thermoplastic epoxy resin or a tacky polyester resin. The general self-adhesive thread cannot withstand the corrosion of freon media, and the self-adhesive layer must have a chemically cross-linked body structure. The self-adhesive paint composed of bisphenol A epoxy and melamine resin has good refrigerant resistance. Corresponding baseline adopts polyester/phenolamine imine or polyimide/thalimine imine composite wire, which can be used for the windings of refrigerant-resistant and sealed compression motors.

Thiophthalamide resin: Compared with other resins, the phthalamide resin has a smooth surface and a lubricating effect, and the friction coefficient is small, which is convenient for high-speed winding. Used in alcohol-soluble polyphthalamide copolymer (nylon 610 and nylon 6 or nylon 66) with a certain amount of polyurethane elastomer and a small amount of thermosetting resin (melamine, etc.) self-adhesive paint coated self-adhesive thread, through Heat bonding after solvent treatment, it still has good bonding strength even at elevated temperature. The deflection coils in TV sets generally require as little as possible the deformation caused by thermal factors and moisture absorption (deformation will cause an increase in the deflection angle), and require the coil to maintain adhesion at a high temperature of at least 130°C. It is difficult to do this with alcohol-soluble copolymer nylon and thermosetting resin. Because alcohol-soluble nylon has adhesive properties, it is easy to cause the wire and the wire frame to stick together and the thermal deformation of the formed coil is serious; while the bonding temperature of thermosetting resin is generally very high (bonding at high temperature makes the baseline and the The performance of amine resin is affected by different degrees), and it is difficult to grasp the degree of curing that is sensitive to the baking temperature (the balance between the flexibility of the magnet wire and the bonding strength). It is reported that nylon copolymers (nylon 12 and nylon 6) containing low melting point nylon 12, non-alcohol-soluble, and not swelled by alcohol at room temperature (nylon 12 and nylon 6) and another group of nylon copolymer factory nylon 6, nylon 6 or nylon 61 . The self-adhesive paint prepared by reacting with nylon 12) is coated on the polyester imide base line, which can be bonded and molded at 160°C and maintain excellent adhesive strength at a high temperature of 130°C. In addition, the surface of the wire is smooth, with little deformation and no stickiness. The self-adhesive paint of phthalamide can also meet the requirements of Class F insulation.
Other resins: In addition to the general baselines, the high temperature resistant baselines of class F and H and other special purpose baselines must be equipped with corresponding self-adhesive layers. The self-adhesive materials of these high-temperature-resistant self-adhesive threads generally use high-temperature resistant resins such as thalidomide and poly-maple. The bonding temperature of this kind of resin is very high, generally above 200 ℃. In addition, thermosetting resin is also used for the self-adhesive layer of the refrigerant-resistant self-adhesive wire in the sealed motor. The comprehensive performance of the enameled wire is excellent. The H-class self-adhesive wire baseline of Rae magnet wire is a polyester/thalidomide imide composite wire, and the self-adhesive layer is a high-temperature-resistant adhesive polyester.