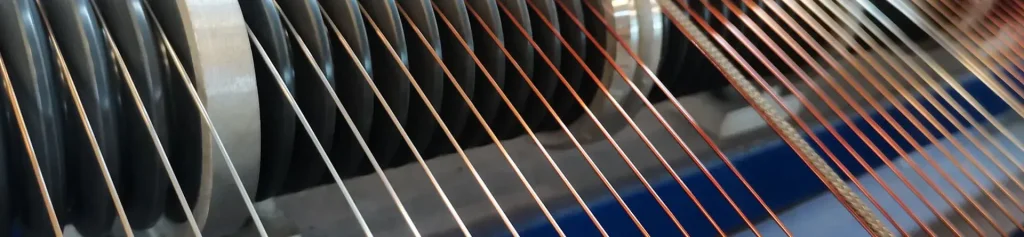
What Is The Difference Between “Magnet Wire” And Regular Insulated Copper Wire (In Using Them As Coil Windings)?
Insulation Type:
Magnet wire is specifically designed with a thin layer of insulation, often a synthetic enamel or varnish-like material, that can withstand high temperatures and is suitable for tight winding in coils.
Coated with a thin layer of enamel (polyurethane, polyester, or similar materials).
Provides electrical insulation while keeping the wire diameter small.
Regular insulated copper wire typically has a thicker insulation layer, which is more suited for general electrical wiring rather than high-temperature or high-frequency applications
Covered with a thicker plastic or rubber insulation, like PVC or Teflon, designed primarily for general electrical wiring to prevent physical and electrical damage.
Electrical Properties:
Magnet wire is engineered to carry currents that generate magnetic fields, with insulation that provides electrical isolation between adjacent turns in a coil, preventing short circuits.
Regular insulated copper wire, while also insulated, is not specifically designed for the high voltage stress and tight winding patterns required in transformers and motors.
Applications:
Magnet wire is used in applications that require the generation of electromagnetic fields, such as in the construction of motor coils, transformers, inductors, choke components, solenoids, and MRI systems.
Regular insulated copper wire is more commonly used for general electrical wiring in residential, commercial, and industrial buildings, as well as in electronic devices and power transmission and distribution networks.
Heat Resistance
Magnet Wire: Enamel coatings are heat-resistant and graded (e.g., 105°C to 220°C), ensuring stability in high-temperature environments.
Regular Insulated Wire: Insulation materials like PVC can melt or degrade at lower temperatures, making them less reliable in high-heat scenarios.
Impact on Coil Windings:
Magnet wire’s thin insulation allows for tighter windings and more turns in the same volume, increasing efficiency in electromagnetic applications.
Regular wire’s thick insulation takes up more space, reducing the density of the winding.