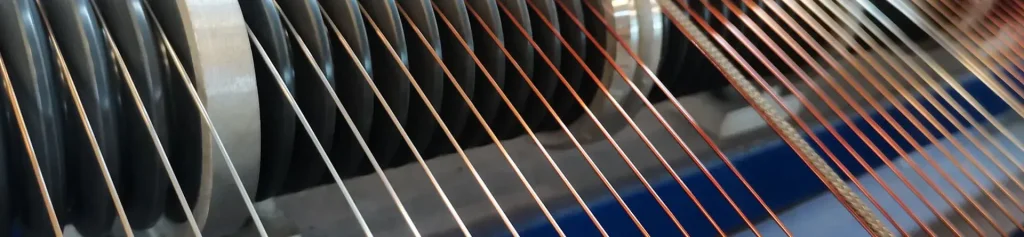
Characteristics of Enameled Wire
GENERAL
Enamelled wire is a metallic conductor insulated with a varnish and generally used for electrical applications. Most times enamelled wire is wound in different shapes of coils to generate magnetic force for motors, transformers, magnets etc. Different types of enamelled wire with the most important differences of characteristics as follows:
Conductor Material for Enamelled Wire
Copper is the standard used conductor material for enamelled wire with excellent conductivity and very good windability. For low weight and larger diameters, Aluminium sometimes can be used as a conductor material for enamelled wire. Because of the difficult contacting of Aluminium wire with problems of oxidation, Copper Clad Aluminium can help to compromise between Copper and Aluminium. For special applications a wide variety of conductor materials for enamelled wire is offered, such as Brass, Silver, Nickel, Gold, Stainless Steel, or alloys of copper for special characteristics like higher mechanical strength or bending performance. In addition, the core conductors can be plated with different materials such as Silver or Nickel.
Bare Wire Diameter Range
LP Industry specializes in fine enamelled wire diameters, starting with 0.008 mm (8 microns), and going up to a diameter of 0.50 mm. Beside the standardized diameters a big variety of special diameters is produced according to customer’s specification. Bare wire tolerances are very important in enamelled wire as they have direct impact on the resistance what again determines the variance of the final coil resistance.
Outer Diameter of Enamelled Wire
International standards like IEC group enamelled wires according to ranges of specific outer diameters. IEC standard for enamelled wire groups the insulation in Grade 1, 2, or 3, NEMA in single, heavy, or triple, and JIS in class 0, 1, 2, or 3. The tolerances in these enamelled wire standards can be further restricted if necessary to design and optimize the wound coils and final products.
Selfbonding Layer
In addition to the base coat insulations described separately, a selfbonding layer can be applied to the enamelled wire, by which the wire will be bonded together for example for bobbinless coils, such as voice coils.
Spool Types for Enamelled Wire
Spool types have to fit to the wire size. Finer enamelled wire sizes are wound on smaller spools, while for heavy sizes of enamelled wire, very large spools can be used. They are important for productivity as larger spools require less spool changes on the winding machines.
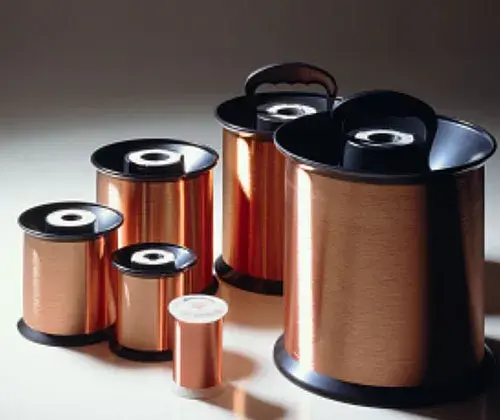
Insulation Types for Enamelled Wire
Elektrisola offers a wide range of different insulations. Polyurethane has the advantage of easy direct contacting by soldering, while Polyester insulations are more resistant against higher temperatures. Thin top coats as Nylon or Polyamidimide may improve certain desired characteristics like mechanical or chemical strength of the enamelled wire.
Enamelled Wire Colors
Colors may be used to differentiate enamelled wire types or enamelled wire diameters, but have the disadvantage of lower technical properties and higher costs.
Lubrication for Enamelled Wire
A defined very low amount of lubrication – mostly special types of paraffin – is applied to achieve excellent windability of the enamelled wire in all winding processes without wire breaks.