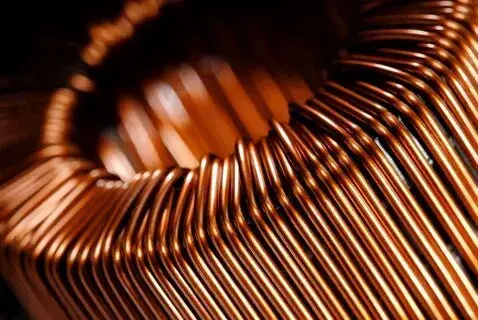
What is Copper Strip Winding?
Copper Strip Windings are composed of lacquered copper wires, which are the basic components of the circuit of every motor or equipment. Lacquered copper and aluminum wires offer advantageous space saving factors as well as high levels of breakdown voltages compared to fiber insulation. The main applications of enamelled copper wire and enamelled aluminium wire are winding of motors and transformers. The voltage of the winding wire depends on the thickness of the insulation layer and can have levels 1, 2 and 3. The higher the grade, the thicker the insulation layer and therefore the higher the breakdown voltage. The temperature rating indicates the temperature of the wire, which has a service life of 20,000 hours. Wires last longer at lower temperatures (about twice as long for every 10 °C drop in temperature). Common temperature classes are 105° C, 130° C, 155° C, 180° C, and 220° C.