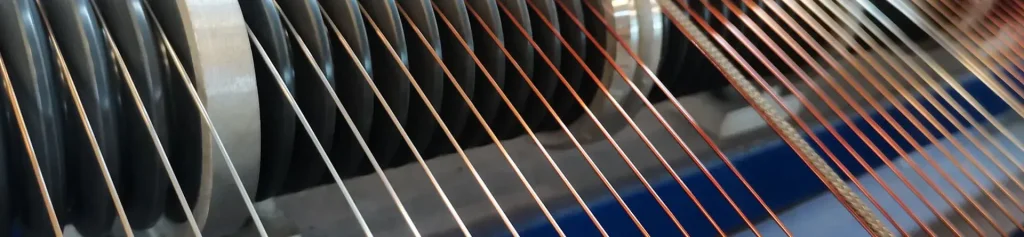
Advantages of Self-Adhesive Enameled Wire
Self-adhesive enameled wire (self-fusion enameled wire) is coated with a layer of self-adhesive paint on the surface of conventional enameled wire. After curing, the self-adhesive paint can be melted by ethanol and high temperature melting to achieve secondary melting, so as to realize the connection between adjacent enameled wires. Gluing.
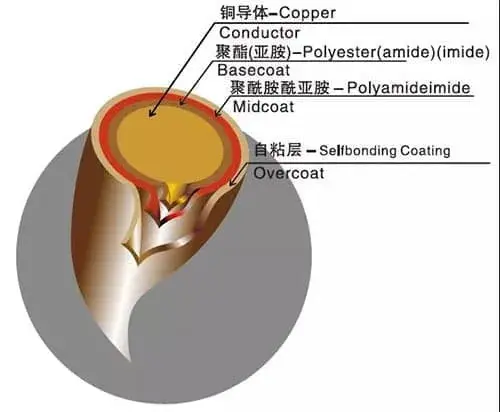
Since most of the bonding of windings adopts the process of dripping paint or dipping paint, the volatilization of the solvent in this process causes serious environmental problems, so self-adhesive wires are used more in developed countries. With the development of my country’s economy and the emphasis on environmental protection, the domestic demand for self-adhesive threads is also increasing.
Alcohol-melted self-adhesive wires are often used in non-skeleton coils such as voice coils and deflection coils. The temperature resistance level is relatively low, and the coil needs to be moved and is sensitive to weight. The enameled wire passes through a felt dipped in alcohol solvent (usually ethanol) before being wound on the model, the melted layer is melted, and the wound coil is naturally air-dried or dried and then shaped.
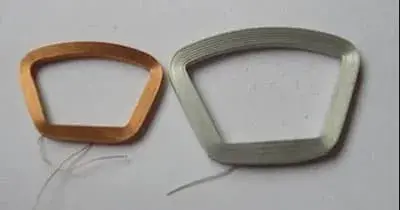
High-temperature self-adhesive enameled wire, using hot air or energizing the conductor to generate heat to achieve secondary fusion, is the most widely used in the stator winding of electric tools.
Most of the self-adhesive coatings are made of polyamide (nylon) or modified aramid. The composite nylon coating on the insulating coating will cause the softening and breakdown performance of the enameled wire to decrease, which is the lower thermoplasticity of nylon. Caused. In power tools, self-adhesive wires are mainly used in the stator, and the stator windings are less impacted. Therefore, even in the case of overload, the force between the wires is small, and the decrease in softening and breakdown performance has almost no effect. However, the excellent ductility of nylon will improve the thermal shock resistance of the enameled wire, thereby increasing the operating life of the insulation at the rated temperature.
In the winding process, when the enameled wire insulation is subjected to a large scratching force, the insulation may be damaged. The rigid structure of the insulation layer may easily cause the insulation to be damaged from the outside to the inside, which leads to the risk of failure between turns. The slipperiness of nylon is beneficial to reduce winding damage. Even in the case of damage, the ductility of nylon can reduce the impact of external force and reduce the damage of the insulation layer, ensuring the reliability of insulation.
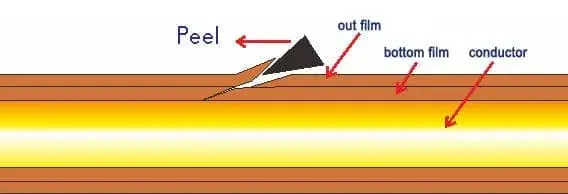
Therefore, taking into account the process damage, the use of self-adhesive wires to make the stator of electric tools, in addition to making outstanding contributions to environmental protection, is also greatly improved than the reliability of the windings using ordinary wires.