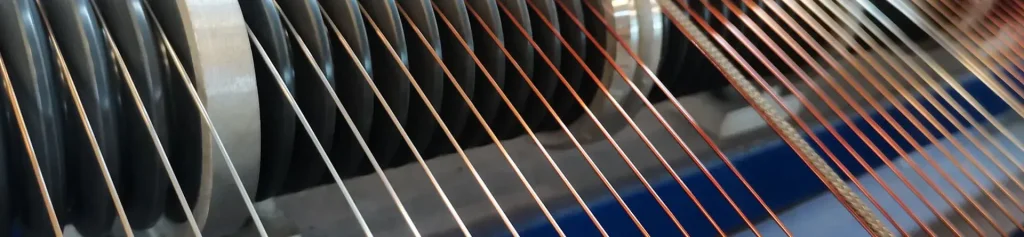
Angle Of Enameled Wire Wrapping: Tips And Key Points
Enameled wire is a common wire insulation material widely used in electronics, electrical and communications fields. During the wire manufacturing process, the correct wrapping angle is critical to ensure the quality and performance of the wire. This article will introduce the angle techniques and key points of enameled wire wrapping to help readers understand how to obtain high-quality wrapping results.
The importance of wrapping angle:
The wrapping angle refers to the angle of the enameled wire around the winding axis. Appropriate wrapping angle can ensure the uniformity, compactness and strength of the wrapping layer, and plays an important role in improving insulation performance, wear resistance and pressure resistance.
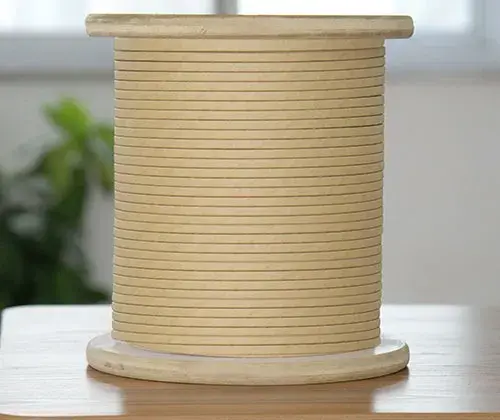
Selection of wrapping angle:
The choice of wrapping angle depends on the specific application and requirements. Generally speaking, common wrapping angles include 90 degrees, 60 degrees and 45 degrees. Several factors should be considered when choosing the right angle:
Insulation requirements: According to the use environment and insulation requirements of the wire, select a wrapping angle that can provide sufficient insulation thickness and strength.
Mechanical strength: The wrapping angle also affects the mechanical strength of the wire. Smaller angles provide greater mechanical strength and are suitable for applications requiring greater wear and pressure resistance.
Wrapping speed: A larger wrapping angle can increase the wrapping speed and improve production efficiency. However, an excessively large angle may result in uneven or loose wrapping.
Adjustment of wrapping angle:
In actual operation, depending on the specific enameled wire performance and mechanical equipment requirements, the wrapping angle may need to be fine-tuned or adjusted. Some common adjustments include:
Equipment adjustment: According to the characteristics and adjustment functions of the wrapping equipment, the wrapping angle can be changed by adjusting parameters such as the position, speed and tension of the wrapping axis.
Guide device: Reasonable design and use of guide devices, such as guide wheels, guide plates, etc., can help control the wrapping angle of enameled wire and ensure the uniformity and tightness of the wrapping layer.
Operating skills: Experienced operators can control the wrapping angle by adjusting the strength and speed of manual operation to make it meet the requirements.
Quality Control and Testing:
For quality control of enameled wire wrapping angle, the following methods can be used:
Visual inspection: Observe the appearance of the cladding through visual inspection or a microscope to check whether there is any obvious unevenness or looseness.
Sampling inspection: randomly select samples from the production line and use appropriate testing equipment to test the thickness, strength and insulation performance of the wrapping layer.
Automatic detection: With the help of advanced detection equipment and technology, automatic wrapping angle detection and control is implemented to improve quality stability and production efficiency.
In conclusion:
The angle at which enameled wire is wrapped has an important impact on the quality and performance of the wire. Selecting the appropriate wrapping angle, adjusting equipment and operating techniques, and conducting quality control and testing are all critical steps to obtain high-quality wrapping layers. By fully understanding the key points and techniques of enameled wire wrapping angle, manufacturers and operators can ensure the production of high-quality enameled wire products with good insulation properties and mechanical strength.