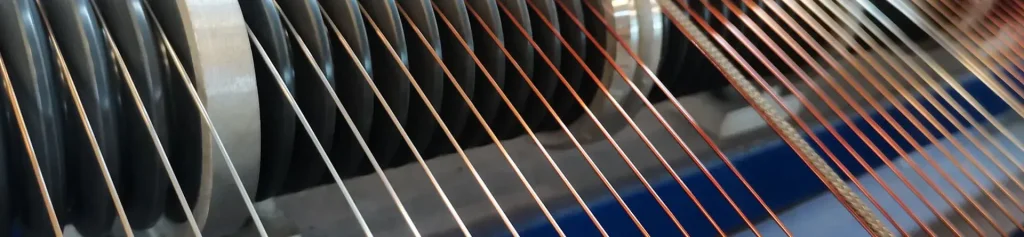
Application of Enameled Wire in Electric Vehicles
With the increasing demand for energy-efficient and environmentally friendly transportation, the development of new energy vehicles (NEVs) has become a trend in the automobile industry. NEVs rely heavily on electrical power, making the quality of electrical components crucial to their performance. Enameled wire, a type of magnet wire coated with a thin layer of insulation material, has become an essential component in the manufacture of NEVs due to its excellent electrical and thermal properties.
Enameled wire is widely used in NEVs to make coils and windings for various components, including motors, transformers, and solenoids. NEV motors require large amounts of enameled wire to create the electromagnetic field necessary for the motor to function. The wire is tightly wrapped around the motor’s stator and rotor, allowing the electrical current to flow through the motor and convert electrical energy into mechanical energy to power the vehicle. Enameled wire is also used to make transformers and solenoids that regulate and control the flow of electrical power throughout the vehicle.
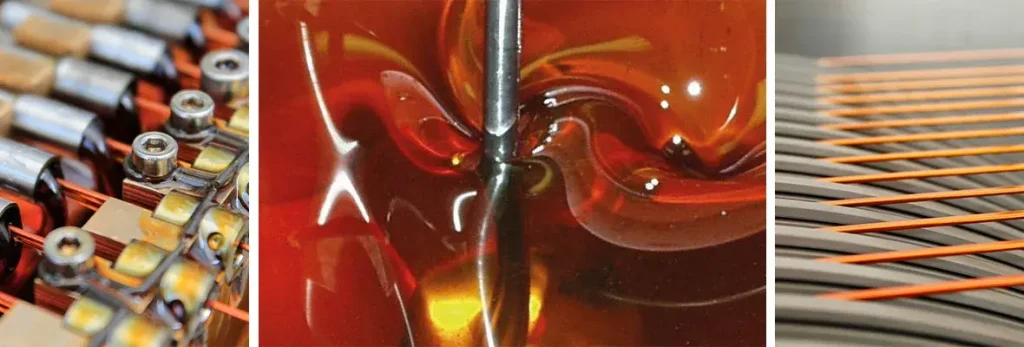
One of the benefits of enameled wire is its high thermal resistance, which allows it to withstand the high temperatures generated by NEV motors without degrading. NEVs require motors with high power densities, which generate significant amounts of heat during operation. If the wire used to make the motor’s coils and windings cannot withstand high temperatures, it can cause the motor to fail or reduce its efficiency. Enameled wire is specially designed to withstand these high temperatures, ensuring the reliability and durability of NEV motors.
Another benefit of enameled wire is its excellent electrical properties, such as high electrical conductivity and low resistance. NEVs require high-performance electrical components that can handle large amounts of current flow while minimizing energy loss. The low resistance of enameled wire allows for efficient current flow, reducing the amount of energy lost as heat during operation. This, in turn, improves the efficiency of NEVs and helps to maximize their driving range.
In addition to its electrical and thermal properties, enameled wire is also highly customizable. It can be made in various sizes, shapes, and colors to suit different NEV applications. The insulation layer on the wire can also be tailored to meet specific requirements, such as resistance to moisture, chemicals, and abrasion.
In conclusion, the application of enameled wire is essential in the manufacturing of NEVs. Enameled wire provides high-performance insulation that allows NEV motors to operate efficiently and reliably, while also allowing for the production of smaller, more efficient transformers and batteries.