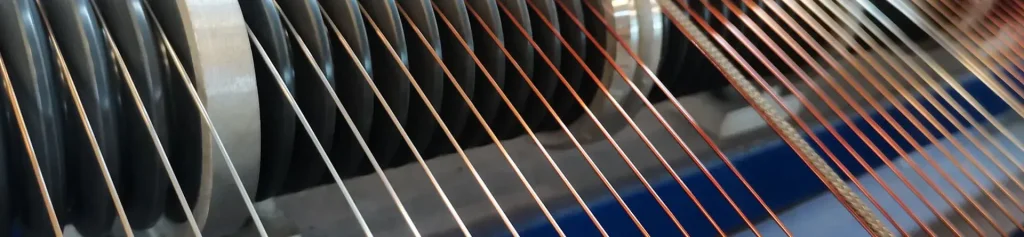
Causes And Elimination Of Frequent Failures Of Heating Pipes Of Enameling Machine Ovens
Since the production of enameled wire is a high energy-consuming process, the stable production mainly relies on solvent combustion to supplement energy, and the wire replacement is a pure heat-absorbing process, so the wire replacement cost is extremely high. In addition, the oxide scale and paint slag generated during the wire change process are easy to move in the furnace cavity with the circulating air flow, and adhere to the surface of the enameled wire to form paint bumps (particles), causing quality fluctuations and it takes a period of time to stabilize. So for the enameled wire factory, a stable order for a single specification is the most pleasing.
There are several equipment in an enameled wire factory that often have the failure of the heating tube of the oven to burn out. Due to continuous production, it cannot be shut down for maintenance. As long as the furnace temperature can be maintained within the allowable range of the process, it is usually until the order is insufficient or the heating tube is open more and more. , The furnace will stop until the temperature reaches the process requirements. After this equipment is repaired, the period of failure will be shortened, and cracks on the inner wall of the oven will occur after one or two years, requiring major repairs.
Cause Analysis
According to experience statistics, the model with the highest failure rate is the equipment for long-term production of first-class film thickness (thin paint film wire for automobile motors) enameled wire, followed by MAG vertical large-size equipment (2.0~4.0mm), vertical Medium size equipment (1.0~2.0mm) and horizontal large size equipment (0.9~1.2mm).
According to the principle of the “zero energy consumption” enameled machine, the heating efficiency of the MAG equipment can be maintained at 40-50% when the second-level film thickness enameled wire is produced on the old equipment with imperfect heat preservation and heat loss prevention measures. For the production of first-class enameled wire with very thin paint film, the solvent that enters the oven per unit time is not enough to maintain the energy balance, and it takes a long time for electric auxiliary heating, which can be as high as 70-80%. High-power heating is maintained for a long time, so that the life of the heating tube is rapidly reduced, and the probability of failure is greatly increased.
For the vertical enameling machine, due to the “chimney effect”, a large amount of hot gas is lost from the upper furnace mouth, and more electric auxiliary heat is required to maintain the heat balance of the oven. When large-size enameled wire is produced, it can generally reach 18-20. The high-speed fan in the cooling section cools a dozen copper wires of 3 to 4 mm from the oven to form a temperature step, thereby forming a cooling rod effect. What’s more frightening is that the main application of large-size lines is generators. The generator market fluctuates greatly throughout the year, and there is no other market to fill in the trough period, so there are frequent shutdowns and line changes. The super-sized wire is a bare copper wire that has not been painted for a long time during the wire change process (the larger the specification, the slower the line speed. There is a standard parameter in the enameled wire industry called VD value, and the speed is inversely proportional to the closeness of the specification) , The heat dissipation capacity is hundreds of times higher than the wire with paint film. If no measures are taken, a large amount of heat will quickly escape to the outside of the oven through a dozen thick copper wires. It is more troublesome to thread the large-size wire with the wire. Operators often leave the wire in the furnace after the machine is shut down, and use it to bring the wire when it is turned on again (only welding or tying the wire once), which will cause difficulty in heating up when the machine is turned on. , The heating time is very long, and the full power heating is overloaded.
The situation of the vertical medium specification and the horizontal large specification equipment is similar. Under the same VD value, the larger the specification, the less solvent enters the oven per unit time, and the greater the electric heating load required.
After clarifying the root cause of the heating tube failure, improve the furnace insulation, reduce the amount of waste discharged, and maintain the faulty heating tube in time to reduce the heating power to below 40%, which can greatly reduce the probability of the heating tube burning. Of course, with the new “zero energy consumption” equipment, due to the good insulation system and higher production speed (which can bring more solvents), the load of the heating tube has been greatly reduced, and the probability of failure of the heating tube burnout is very low.