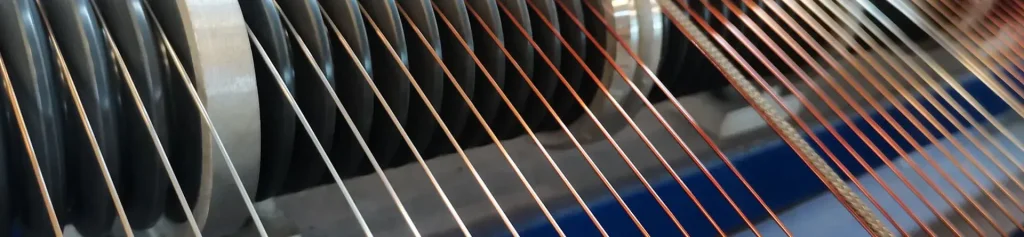
Class 105 Polyvinyl Acetal Enameled Rectangular Copper Wire China
- Width: 2.00 mm, max. 16.00 mm
- Thickness: min.80 mm, max. 5.60 mm
- Thermal performance
- Electrical properties
- Mechanical properties
- Spools or Containers:The wire should be evenly and compactly wound on spools or placed in containers. No spool or container should contain more than one length of wire unless agreed upon by the purchaser and supplier.
- Coils:For wires delivered in coils, the dimensions and maximum weights should be agreed upon by both parties. Additional protection for coils should also be specified.
- Motor Windings: Used for the stator and rotor windings in motors.
- Transformers: Applied in the primary and secondary windings of transformers.
- Relays: Used as coil material in various relays and solenoids.
- Electronic Components: Utilized in electronic components requiring high insulation performance, such as sensors and transformers.
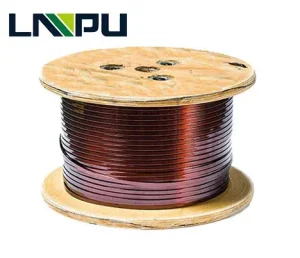
IEC 60317 outlines the specifications for Class 105 enamelled rectangular copper winding wire with a primary coating made of polyvinyl acetal resin. This resin can be modified as long as it retains the original chemical identity and meets all the specified requirements for the wire.
Note: A modified resin is one that has either undergone a chemical change or includes one or more additives to enhance specific performance or application characteristics.
Class 105 represents a thermal classification that mandates a minimum temperature index of 105 and a heat shock temperature of at least 155°C. However, the temperature index in degrees Celsius does not necessarily indicate the recommended operating temperature for the wire. The appropriate operating temperature will depend on various factors, including the type of equipment in which the wire is used.
The range of nominal conductor dimensions:
Main specifications
1.1 Thermal rating: Class 105 means the wire can operate at temperatures of 105°C for a long time without significant aging or performance degradation. This is especially important for equipment such as motors and transformers that need to operate in high-temperature environments.
1.2 Thermal shock test: The wire needs to pass the thermal shock test under high temperature conditions to ensure that the insulation layer will not crack or peel during temperature changes.
2.1 Insulation resistance: Polyvinyl acetal enameled wire must have high insulation resistance to prevent current leakage. Standards require that the insulation resistance measured under specific conditions must reach a specified minimum value.
2.2 Dielectric strength: The insulation layer must be able to withstand high voltages without breakdown. A certain dielectric strength value is usually required to ensure safety in high-voltage applications.
3.1 Tensile Strength and Ductility: Wire must have sufficient tensile strength and ductility to withstand the mechanical stresses during manufacturing and installation.
3.2 Flexibility: Polyvinyl acetal enameled wire needs to have good flexibility so that it can be bent and wound without damaging the insulation layer during use.
4. Adherence
4.1 Mandrel winding test
The coating shall show no crack after the wire has been bent flatwise and edgewise on a mandrel with a diameter as specified in table below:
Mandrel winding
Wire bent on | Mandrel diameter | |
Width | Sizes up to and including 10 mmSizes over 10 mm | 2xwidth3xwidth |
Thickness | All dimensions | 2xthickness |
4.2 Stretching test
The wire shall be stretched by 20 %.
The distance of loss of adhesion shall be less than 1*width
Packaging and Handling
Proper packaging is crucial to maintaining the wire’s properties:
Applications
Polyvinyl acetal enamelled rectangular copper wire of Class 105, compliant with IEC 60317-0-17, is widely used in various electrical and electronic devices, including but not limited to: