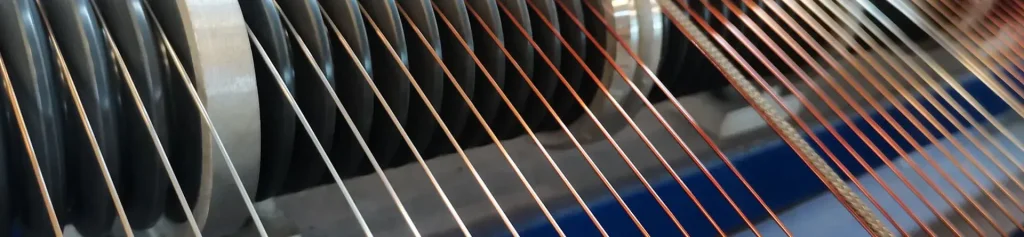
Coil Winding in Dry Type Transformers: Ensuring Efficiency and Reliability
Coil winding is a crucial process in the manufacturing of dry type transformers. Dry type transformers, also known as cast resin transformers, are widely used in various industries and applications due to their numerous advantages over traditional oil-filled transformers. The coil winding process plays a significant role in ensuring the efficiency, reliability, and performance of dry type transformers.
Coil winding involves the careful arrangement of copper or aluminum conductors in a predetermined pattern to form the primary and secondary windings of a transformer. The winding process is carried out with precision and attention to detail to ensure the desired electrical characteristics of the transformer. The primary winding is connected to the power source, while the secondary winding delivers the transformed voltage to the load.
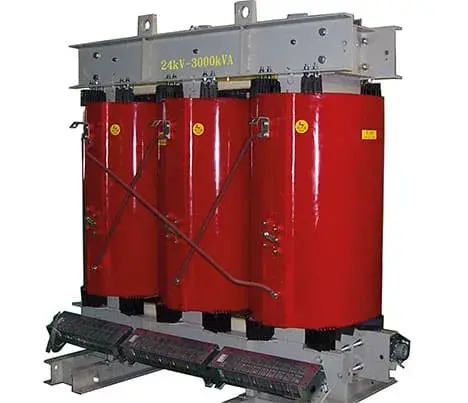
One of the key considerations in coil winding is the selection of the appropriate conductor material. Copper is the most commonly used material due to its excellent electrical conductivity and thermal properties. However, aluminum is also gaining popularity as it offers a more cost-effective solution while maintaining adequate conductivity. The choice of conductor material depends on factors such as the transformer’s power rating, application requirements, and budget constraints.
The coil winding process begins with the selection of the conductor wire. The wire is typically insulated with materials such as enamel or fiberglass to prevent electrical short circuits and ensure proper insulation. The wire is then wound around a cylindrical or toroidal core, depending on the transformer design. The winding pattern and number of turns are carefully calculated to achieve the desired voltage transformation ratio.
During the winding process, it is crucial to maintain consistent tension and spacing between the turns to avoid any electrical or mechanical issues. Special attention is given to prevent any overlapping or crossing of the wire turns, as this can lead to short circuits and reduce the transformer’s overall performance.
Once the winding is completed, the coils are impregnated with a resin compound to provide insulation and protection. The resin is carefully applied to fill the gaps between the windings and ensure the entire coil is encapsulated. This resin impregnation process enhances the transformer’s thermal stability, moisture resistance, and mechanical strength.
The coil winding of dry type transformers requires skilled technicians with expertise in electrical engineering and transformer manufacturing. Advanced machinery and computer-aided design (CAD) software are utilized to precisely calculate the winding parameters and ensure accurate and efficient coil winding.
In conclusion, coil winding is a critical process in the manufacturing of dry type transformers. The careful arrangement of conductors and precise winding techniques determine the transformer’s electrical characteristics and performance. With advancements in technology and the use of high-quality materials, dry type transformers continue to provide reliable and efficient power distribution solutions in various industries.
Welcome to see the magnet winding wire in lpnamelwire.