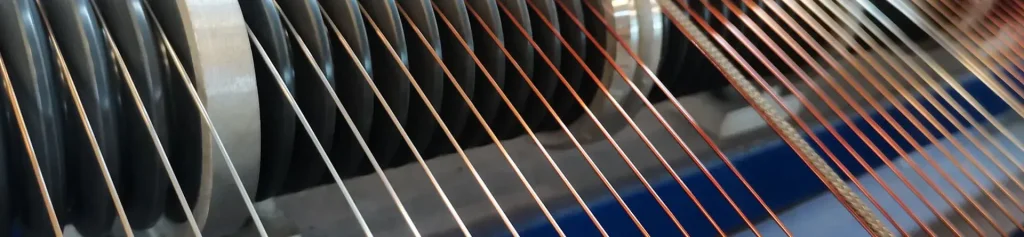
Copper Wire And Aluminum Wire Used In Transformer
A transformer is a device that transfers electrical energy from one circuit to another through its coils (windings). The properties needed for motor windings are similar to those needed for transformers, but with the additional requirement to withstand mechanical vibration and centrifugal forces at operating temperatures.
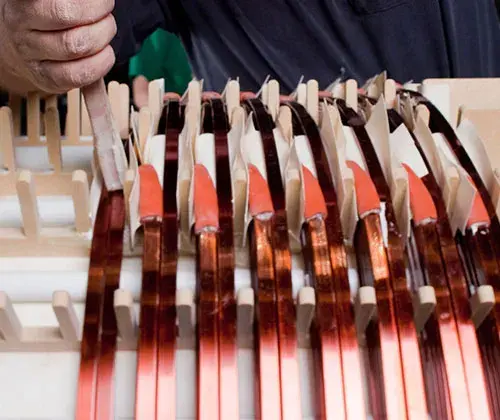
Transformer windings are normally made from copper but aluminium is a suitable competitor where weight and first cost are decisive factors.
In North America, aluminium is the predominant choice of winding material for low-voltage, dry-type transformers larger than 15 kilovolt-amperes (kVA). In most other areas of the world, copper is the predominant winding material. Purchasing decisions are generally a function of loss valuations expressed in currency per kilowatt.
Copper magnet wire used for the manufacture of transformer windings is in the form of wire for small products and strip for larger equipment. For small products, the wire must be strong enough to be wound without breakage, yet flexible enough to provide close-packed windings. Strip products must be of good surface quality so that insulating enamels do not break down under voltage. Good ductility is essential for the strip to be formed and packed while good strength is needed to withstand the high electro-mechanical stresses set up under occasional short-circuit conditions. Copper winding wires in transformers are compatible with all modern insulation materials, such as lacquer and enamel. Lacquers permit the close spacing of windings to give best efficiency in the coils.
A major engineering reason to choose copper windings over aluminium is space considerations. This is because a copper-wound transformer can be made smaller than aluminium transformers. To obtain equal ratings in aluminium wire transformers, a 66% larger cross-sectional area is required than for copper conductors. However, the use of larger-sized conductors results in the winding strength of aluminium being nearly equivalent to that of copper windings.
Connectivity is another important benefit of copper-wound transformers, as the oxide coating on the surface of aluminum makes soldering or otherwise connecting with it more difficult. Cleaning and brushing with a quality joint compound to prevent oxidation is not necessary with copper.