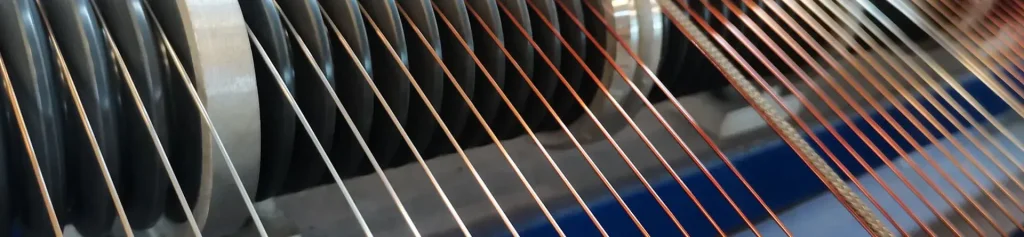
Enameled Wire Knowledge Collection
Q: Why is copper wiring safer than aluminum wiring?
A: Both copper and aluminum wiring are acceptable when properly installed per National Electric Code guidance.
The “aluminum is not safe” theme arose out of incorrect installation of aluminum wiring into fixtures whose connecting hardware was not designed for aluminum wiring… allowing the wiring to decouple, arc, possibly start a fire.
Most fixture manufacturers presently provide dual-rated connection hardware.
Many highrise buildings use aluminum wiring safely accordingly… as aluminum is lighter weight than copper.
Q: Apart from copper and aluminum, what other metal can be used to wire a transformer?
A: In principle, any metal can be used to wire a transformer, but it has to be insulated. Roughly 70% of the elements in the periodic table are metals, so you would think that you might have a wide variety to choose from. But most aren’t suitable for one reason or another. Mercury is a liquid at room temperature. Sodium is too reactive, Bismuth is too brittle, etc.
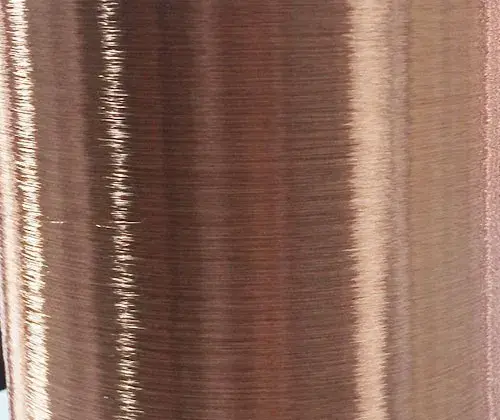
Q:What are enameled aluminum magnet wires?
A: Enameled aluminum magnet wires are a type of electrical wire used in a variety of applications. These wires are composed of aluminum which has been wrapped in a thin layer of enamel insulation. This insulation provides protection from environmental elements such as moisture and chemicals, and also helps to keep the wire from shorting out. The enamel layer is typically made up of a polyester or polyurethane material and is capable of withstanding temperatures up to 180 degrees Celsius.
Enameled aluminum wires are often used in motors, transformers, coils, and generators. They are a popular choice for these types of applications due to their excellent electrical properties, as well as their flexibility and durability. The aluminum core of the wire offers superior conductivity, allowing for more efficient electricity transfer, while the enamel insulation provides an extra layer of protection and insulation.
Q: What is the difference between copper wire and magnet wire?
A: Copper wire is a widely used standard type of wire, It has a very low resistance (ohms/foot). This allows it to carry higher amps with out getting to hot. Ohms/foot is a however a negative effect. Regardless, read on.
Magnet wire is used to create the magnetic effect. Magnet wire is copper wire with a special enameled coating. The coating acts as insulator, this allows the wire to be wrapped many times in a coil (circle). Maxwell showed us that when wire is wrapped in a coil the electrons passing thru the wire will create a magnetic field perpendicular to the current flow. The action of multiple windings multiplies the magnetic effect. In physics this is referred to as the right hand rule. (google it). A common device using this process is the electo-magnet. An audio speaker is an electro-magnet with a paper cone attached. The music in the form of a varying voltage drives the magnet to move the paper cone, our ears will pick up these audio variations of the air.
So the answer to your question; ‘the enameled insulation”. btw, the thinness of the enamel increases efficiency, decreasing the overall size, more wraps per cubic centimeter, more magnetic effect, denser magnetic filed, ie. strength.
Q: Why is copper wire preferred over aluminium and iron wire for household work?
A: In the 1960’s. home builders began replacing copper wiring with aluminum wire which was much cheaper. While aluminum is an excellent conductor of electricity, it created problems when it was used for household wiring. Aluminum often didn’t connect securely to the electrical fixtures (receptacles, ovens and air conditioners) then being used. Corrosion of the aluminum also created a bad connection and caused fires, and the wire sometimes cracked as it aged also causing problems. After there were a large number of problems with the aluminum wire, the builders went back to copper wire. There have been a number of improvements in both the hardware used with aluminum wire and better alloys were developed in the metal itself, and many builders are back to using aluminum wire. Iron wire is a very poor conductor of electricity, and is unusable for that reason.
Q: Why does aluminum wire spark when connected to copper wire?
A: Generally, it’s because of the potential (voltage) difference between the two wires. It also happens that way between two copper or two aluminum or two coat hangers with similar conditions.
Q: What is the effect of painting on enameled wire?
A: This is because the enameled wire is coated with a special layer of paint. It contains oils, resins, pigments, fillers and solvents. In order to meet the requirements of electrical insulation, the film structure of electrical insulation varnish is different from ordinary paint, it has large resistance coefficient, good thermal conductivity, and has strong mechanical properties and good moisture resistance. It is precisely because the resistance of the enameled wire is large, so its insulation performance is good.
Insulating paint is a kind of special paint in paint. Insulating paint is an important insulating material based on high molecular polymer, which can be cured into an insulating film or the whole insulation under certain conditions.
Q: Which electric wire is best, copper or aluminium?
A: Actually, it depends upon application. Copper is more conducting than aluminium but is heavier and costlier than aluminium. Even if we increase the cross section of aluminium wire to maintain the same resistance and the same power loss as copper wire, its weight is 70% of copper and hence decidedly cheaper than copper.
However, when we switch over from copper to aluminium, it means increased size and reduced overload capacity due to lower melting point of aluminium.
Considering the above pros and cons for copper and aluminium, copper is preferred material for electrical machines. On the other hand, aluminium (with steel reinforcement) is the preferred material for power transmission.
Q: Which is more stable, copper wiring or aluminum wiring?
A: Assuming you are talking about normal house wiring, then copper is the ONLY safe way to go. It is difficult to make a good, stable connection with aluminum for a couple reasons. First, aluminum oxidizes instantly on contact with oxygen, so even if you scrape, sand, buff an aluminum wire to clean it, by the time you connect it, you already have an oxidized film on the wire. If you are going to connect it to copper – wire nut, saddle connector, etc. then you must use an anti-corrosion compound in the joint to insure a good connection. If any moisture gets into the connection than, having an electrical current flowing through two dissimilar metals some electrolysis will occur greatly increasing the corrosion problem.
Second, aluminum cold-flows under pressure so when you connect it to a screw terminal such as a circuit breaker or switch, or an outlet the screw will put pressure on the aluminum wire and, after time, the aluminum will cold-flow away from the pressure causing a slightly loose connection – which can eventually lead to overheating and nasty stuff like fires. The fact the the aluminum and whatever it connects to expand and contract at different rates and to different degrees adds to the creep problem.
In industrial situations, such as power line distribution, aluminum wire and cable can be used, but provisions still must be made to alleviate the corrosion and cold-flow problems.
Q: What is the minimum thickness of enamel wire to withstand 50A current?
A: Magnet wire or enameled wire is a copper or aluminium wire coated with a very thin layer of insulation. It is used in the construction of transformers, inductors, motors, speakers, hard disk head actuators, electromagnets, and other applications that require tight coils of insulated wire.
The wire itself is most often fully annealed, electrolytically refined copper. Aluminium magnet wire is sometimes used for large transformers and motors. The insulation is typically made of tough polymer film materials rather than enamel, as the name might suggest.
Thicker wires have a larger diameter and cross section area, thus has a lower resistance for the same wire length, and can handle higher current.
Each wire has resistance, and the resistance has to do with the material’s conductivity, wire thickness and wire length.
thinner wire = more resistance
longer wire = more resistance
Wires with more resistance will cause more voltage drop and delivers less power.
When drawing more current than the wire can handle, it will simply start to heat up due to resistance, and eventually melt. It also becomes the bottleneck in your power system and could struggle to deliver the power to your ESC/motors.
Q: What is the difference between “dead soft” & “half hard” copper wire?
A: Dead soft and half hard are degrees of hardness in wire. Often, these terms are used for wire that is used in jewelry making.
Dead soft wire is, as it’s name implies, soft and offers little resistance to being shaped. It bends easily and takes well to being shaped into flowing curves.
Half hard wire is a bit stiffer. It is tougher to bend, but holds it’s shape better. Half hard is better for sharp bends.
Copper wire reacts to being bent by getting stiffer. This is called work hardening. Each time the wire is flexed, it gets a little stiffer. Therefore, dead soft wire can be stiffened to half hard by working it.
The only way to soften it is to anneal it. This requires heating the wire to it’s annealing temperature and then allowing it to cool.
Q: Can a copper wire be used for aluminum wiring?
A: Copper wire is better, but more expensive than aluminum wire, as copper doesn’t corrode, aluminum does. The convenience is the reason that most house wire is copper.
The cost is the reason that most large conductor wire is aluminum, but you have to treat the ends with special compounds to keep the wire from corroding at the terminals.
Copper wire needs a smaller diameter to carry the same current. #14 solid copper will carry 15A, but you need #12 aluminum, #14 aluminum will only carry 12A.