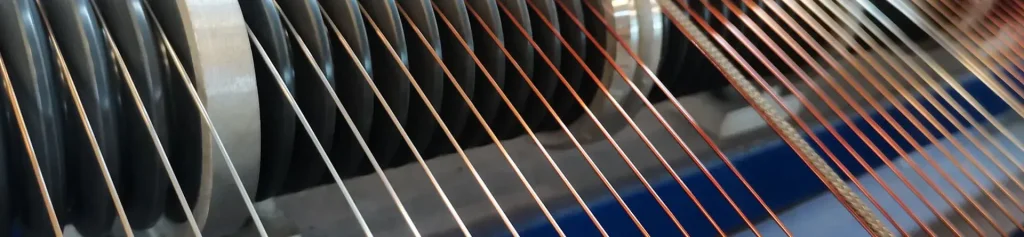
Enameled Wire Question and Answer Collection
- Aluminum enameled wire is simpler to form coils compared with copper enameled wire, because the surface of aluminum enameled wire features a strong oxide film, which has good insulation effect and long service life.
- The most important advantage of using aluminum wire is light 1/3 due to copper wire, greatly reducing cost , and straightforward to connect to solid. It also can reduce the operation of freight and transportation.
- microwave transformer;
- It’s used for creating windings that need light weight, relatively high conductivity and good heat resistance, especially for winding high frequency signals.
- High frequency transformer, common transformer, inductor coil, motor, household motor and electromagnetic wire for micro motor.
- Small motor rotor and other enameled wire.
- Display deflection coil with electromagnetic line;
- Electromagnetic wire for degaussing coil;
- Other special electromagnetic lines
Q: What are the several properties of enameled wire?
A:
1. Appearance
The surface must smooth, shiny metallic colors and no scratch. The surface coating film must not sticky at room temperature.
2. Flexibility
Enameled copper wire must be stretched and bent when tested by pulling or lapping. There must no cracks of the coating
film.
3. Adherance
The wire coated with the adhesive and no cracks in the coating film.
4. Dielectric break down voltage
Dielectric break down voltage must not less than the standard of electric voltage enameled wire. Specification of enameled
wire can be referred to the industry standard (ISO) or refer to the standard of Japanese Industrial Standard
(JIS C 3202 &. JIS C 3003).

5. Heat-shock proof
The enameled wire must resist to the heat change immediately by without any fracture of the coating film.
6. Conductor resistance
Enameled copper wire must have conductor resistance not exceed the specified maximum resistance. The conductor
resistance does not exceed the maximum set by the resistance of each wire coated varnish. Please refer to the industry
standard (ISO) or refer to the standard of Japanese industrial standard (JIS C 3202 & JIS C 3003).
7. Deterioration proof
Wire coating must be resistant to deterioration tested by pulling and stretching (Elongation) without any fracture of the
coating film.
8. Softening proof
Enameled copper wire with a diameter from 0.20 mm. of the bare wire must have flexibility without a short circuit.
Please refer to the industrial standard (ISO) or refer to the standard of Japanese industrial standard
(JIS C 3202 & JIS C 3003).
9. Solvent proof
Enameled copper wire must be resistant to solvents by without abrasion of the coating film. Please refer to the industrial
standard (ISO) or refer to the standard of Japanese industrial standard (JIS C 3202 & JIS C 3003).
10. Reagent proof
Enameled copper wire must be resistant to reagents by without abrasion of the coating film. Please refer to the industry
standard (ISO) or refer to the standard of Japanese industrail standard (JIS C 3202 & JIS C 3003).
11. Insulating-oil proof
Enamelled copper wire must resistant to oil insulation by without abrasion of the coating film. Please refer to the industry
standard (ISO) or refer to the standard of Japanese industrial standard (JIS C 3202 & JIS C 3003).
12. Solderability
Enameled wire must be coated solder with the coating film. This section is for the only certain kinds of varnish coated wire.
13. Pin hole
Porous enameled wire must not exceed the number of specified pin holes. Please refer to the industrial standard (ISO) or
refer to the standard Japanese industrial standard (JIS C 3202 & JIS C 3003).
Q: How do I fix a cable consisting of six different colored enameled wires?
A:
1 remove power from the cable
2 cut and remove the damaged section of cable.
3 strip 1/4 inch insulation from both the ends of the cable. You may want to cut the cable to different lengths in a stair step fashion.
4 slide 1/2″ pieces of polyolefin heat shrink over each wire and a larger piece of heat shrink over the entire cable.
5 solder each wire to it’s matching wire.
6 slide the heat shrink so it covers each splice
7 shrink the heat shrink pieces with a heat gun.
8 slide the large heat shrink so it covers all the splices and exposed enameled wires.
9 shrink the large heat shrink pieces with a heat gun.
Q: What’s the difference between an enameled aluminum wire and an enameled copper wire?
A: Copper is more conductive, requiring smaller cross-section for a given current and easier to solder or otherwise connect.
Aluminum is less conductive, requiring larger cross-section for a given current. Despite this, it is cheaper than copper.
Q: What’s a good size heat shrink tube for a 30 AWG enameled magnet wire wrapped and soldered on a 26 AWG enameled magnet wire?
A:
1. More variety of products: As the demand of the downstream industry of magnet wire becomes more diversified, as well as the product upgrade and technology update of the downstream industry, it will bring new product demand in the magnet wire industry, making the variety more abundant. With the improvement of insulating materials and the development of new products, the range of thermal grades has been expanded, and the varieties of the same thermal grade have increased to meet the needs of different industries.
2. Intensified industry integration and large-scale development: At present, there are many magnet wire manufacturers in my country, and their production capacity ranges from more than 1,000 tons to 100,000 tons per year. Among them, aluminum-based magnet wire manufacturers have a production capacity of more than 10,000 tons. And the homogeneity of its products is more serious, which makes the competition in the electromagnetic wire industry more sufficient. With the slowdown of my country’s economic growth, intensified competition in the electromagnetic wire industry, rising labor costs and higher requirements for environmental protection, small and medium-sized enterprises in the industry will face greater operating pressure. At the same time, because this industry is a capital-intensive industry, it has high capital requirements and has economies of scale. Therefore, the market share of large-scale electromagnetic wire manufacturers will further increase in the future, and the market concentration will increase accordingly.
Q: What’s the best (cheap) way of stripping enamel off of a magnet wire?
A: The old stuff (usually a dark brown color) was a bit difficult (I used to use sandpaper, or a very sharp blade used like a scraper), but contemporary insulation will just “go away” when you hit it with a hot enough soldering iron.
Q: What property of a wire increases when it is made longer?
A: This sounds like a homework question, but it does address the very serious issue of voltage drop, which is directly proportional to conductor length, current and material resistivity. This means that the longer a wire is, the more resistance it will have and the more voltage (potential) it will lose over that distance.
Decreasing the current will cause less voltage drop, but also provide less power to the load, but increasing the cross-sectional area of the wire, or using more conductive material (less resistivity), will also ameliorate voltage drop, allowing a longer conductor (so now you have a Longer AND thicker cable to carry the voltage and current you need).
Nikola Tesla found a way around this for us last century with Alternating Current and the transformer: by converting a generated voltage into a much higher transmission voltage, transmission current was decreased proportionally, but total electrical power remained the same. At the point of consumption, we then use distribution transformers to step voltage back down to practical common level, but since all that electrical power is still available, less voltage means proportionally greater current. Voltage drop in a conductor does not depend on the voltage applied to the conductor, so higher transmission voltage does not affect voltage drop, but the decreased current makes voltage drop much more manageable, almost negligible.
Q: How do I remove enamel from a wire?
A: Well this really depends on what your calling enamel? Are we talking about paint or enamel like on a bathtub ? Are we I’m going to assume your talking about the clear coat on copper wire some times seems to protect it for oxidation. The second question is just how well do you want to remove it ? You can scrape it off but that’s not a good job so you’ll probably want to take some paint remover to it but that is kinda expensive. The last option is to burn it off . The only problem is the fumes and just how it will effect the metal I don’t know. At any rate it’s going to be black and chard . If this is for recycling you might get away with the burning of the enamel. Chemicals to remove the enamel will be acetone , xylene , Xyloile or paint remover what ever is cheapest. These chemicals are very flammable and have a low flash point which means you don’t work with it with out Chemical gloves away from flames of any type in a well ventilated area . You should breathe these chemicals and if they get on you flush them off with water fast. They will give you a chemical burn. You shouldn’t leave these chemicals in direct sun they will evaporate fast and my catch on fire if they get too hot. A hot shed isn’t the ideal place for these chemicals and certainly not near a water heater.
Q: What is the effect of painting on enameled wire?
A: Insulating effect.
This is because the enameled wire is coated with a special layer of paint. It contains oils, resins, pigments, fillers and solvents. In order to meet the requirements of electrical insulation, the film structure of electrical insulation varnish is different from ordinary paint, it has large resistance coefficient, good thermal conductivity, and has strong mechanical properties and good moisture resistance. It is precisely because the resistance of the enameled wire is large, so its insulation performance is good.
Insulating paint is a kind of special paint in paint. Insulating paint is an important insulating material based on high molecular polymer, which can be cured into an insulating film or the whole insulation under certain conditions.
Q: What is the advantage of a flat enamelled aluminium wire?
A: Enamelled Aluminum Wire / Enamelled Copper Wire are primarily utilized in three sorts of applications – in transformers to rework one quite electricity into other forms. Aluminum Enameled Wire is utilized in motors to rework electricity into energy. Enameled Aluminum Magnet Wire and Enamelled Copper Magnet wire are used because the wire in electromagnets that use electricity to get a magnetic flux. Like other wire, Aluminium & Copper Enamel Magnet Wire is assessed by diameter or area, temperature class, and insulation class. Copper has better conductivity than aluminium, so its heat losses are lower.
The advantages of enameled aluminum wire:
Application areas: