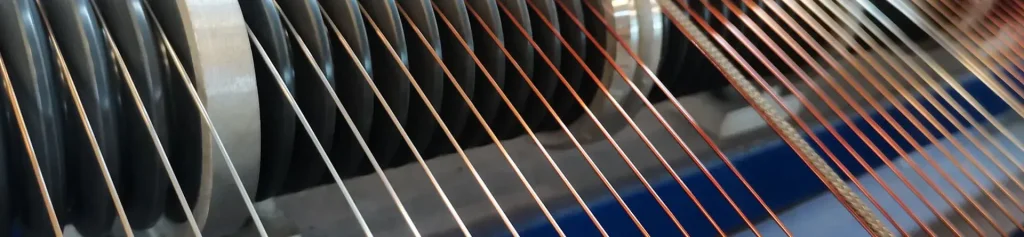
Heat Resistance of Enameled Wire
With the development of science and technology, people pay more and more attention to the improvement of insulation materials and insulation technology for electrical appliances, and wire enamel plays an important role in it. At present, motors and electrical appliances are developing in the direction of miniaturization, light weight, and high performance, and the requirements for the heat resistance level of insulating materials are also getting higher and higher. After the development of motors and electrical appliances in the direction of small size and high power, enameled wires are required to be made thinner and thinner.
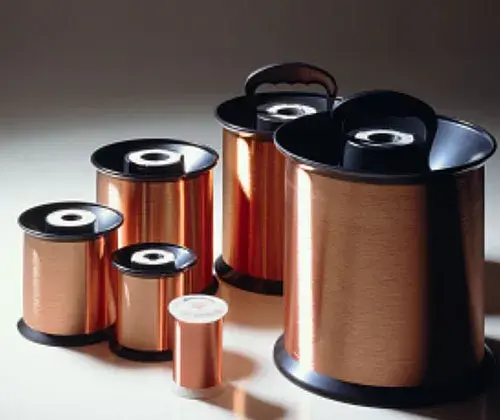
Coupled with the shortage of copper raw materials, aluminum is used instead of copper in some electrical appliances, resulting in an increase in the thermal load of enameled wires. Therefore, enameled wire needs better heat resistance, which requires enameled wire paint to have better heat resistance, or to have a certain special thermal performance, and then to meet the requirements by coating composite enameled wire. Heat-resistant enameled wires generally use polyimide, polyester amide imide, polyamide imide, polyester imide, heat-resistant polyester, etc. Due to the high cost, the first two are only used in some special occasions. The cost of polyamideimide is also very high, and it is generally used as a topcoat for composite enameled wires. Polyesterimide has excellent comprehensive properties and can be used alone or as the inner coating of composite wires, so it is widely used. Heat-resistant polyester has higher softening breakdown than polyesterimide, and it is used as the inner coating of composite enameled wire, and the enameled wire coated with polyamideimide as the outer coating has high softening breakdown and thermal shock , At the same time, the polyester resin is easy to dissolve, the process is easy to control, and the surface of the enameled wire produced is good.
The heat resistance of enameled wire includes thermal shock and softening breakdown tests. The thermal shock of the enameled wire is the ability of the paint film of the enameled wire to withstand heat under the action of mechanical stress. Factors affecting thermal shock: paint, copper wire, enamelling process.
There are several nominal temperature ranges (thermal classes), listed with the basis on which the enamel is made, for example:
155-180°C – Polyurethane (good solderability at 370-390°C)
180-200°C – Polyamideimide (good thermal and chemical resistance, solderable above 470°C)
220°C – polyamidimide (good thermal and mechanical resistance, not solderable through enamel)
240°C – aromatic polyimide (very good thermal, chemical and radiation resistance, not solderable through enamel)