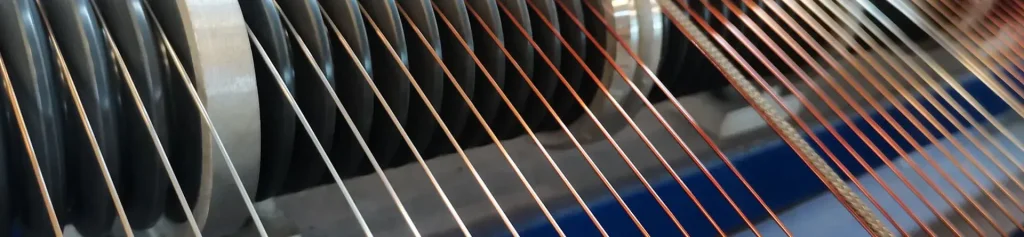
Impact of Enamel Coating on Copper Wire
- Electrical Insulation:
- Primary Function: The enamel coating serves as an electrical insulator. This is vital in preventing short circuits, especially in applications where wires are wound closely together, such as in transformers, inductors, motors, and electromagnets.
- Dielectric Strength: Enamel coatings provide high dielectric strength, allowing wires to be wound tightly without risking electrical breakdown.
- Mechanical Protection:
- Abrasion Resistance: The enamel coating protects the copper wire from mechanical damage such as abrasions and cuts during handling and installation.
- Environmental Protection: The coating shields the copper from environmental factors like moisture, chemicals, and corrosive gases, which can lead to oxidation and corrosion.
- Thermal Stability:
- Heat Resistance: Enamel coatings are designed to withstand high temperatures, which is essential for applications involving significant heat generation, like motors and transformers.
- Thermal Aging: High-quality enamel coatings resist thermal aging, thereby prolonging the wire’s lifespan even under continuous thermal stress.
- Intrinsic Conductivity:
- Unaffected Core: The copper wire’s intrinsic electrical conductivity remains unchanged by the enamel coating. Copper’s low electrical resistance and excellent conductivity are preserved.
- Surface Effects:
- Skin Effect: In high-frequency applications, current tends to flow near the surface of the conductor. The thin enamel coating has a negligible impact on this effect but ensures that adjacent turns of wire do not short-circuit.
- Heat Dissipation:
- Thermal Insulation: While the enamel provides some thermal insulation, it can also impede heat dissipation. Proper thermal management must be considered in the design to ensure effective heat removal from the wire.
- Wire Handling and Winding:
- Tighter Winding: The insulation allows wires to be wound more tightly, maximizing space efficiency in coils and windings. This is particularly important in applications requiring high power density.
- Flexibility and Durability: Enamel-coated wires are more flexible and durable compared to bare wires, facilitating easier handling and installation.
- Polyurethane:
- Ease of Soldering: Often used where soldering is required without prior removal of the coating.
- Polyester:
- General Use: Commonly used for general-purpose applications due to its good balance of properties.
- Polyamide (Nylon):
- Abrasion Resistance: Provides superior abrasion resistance and is often used as a topcoat over other enamels.
- Polyimide:
- High-Temperature Applications: Suitable for extremely high-temperature environments due to its excellent thermal stability.
- Polyesterimide:
- Chemical Resistance: Offers good thermal and chemical resistance, suitable for more demanding applications.
The enamel coating on copper wire, often referred to as magnet wire, is a crucial component in many electrical and electronic applications. Here’s an in-depth look at its roles and effects:
Purpose and Benefits of Enamel Coating
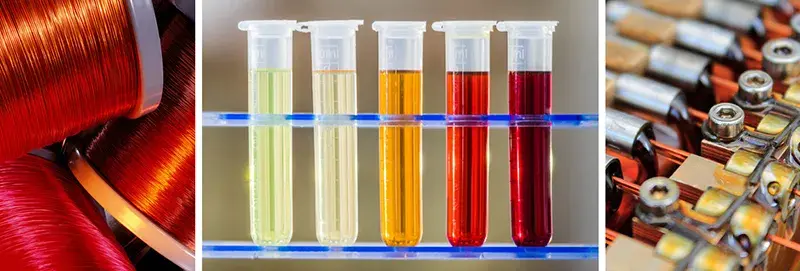
Impact on Conductivity and Performance
Types of Enamel Coatings
Conclusion
The enamel coating on copper wire is indispensable for its insulation, protection, and durability benefits, especially in complex and high-stress electrical applications. While it does not alter the copper’s inherent conductivity, it ensures that the wire performs reliably and safely in various environments, enhancing the overall efficiency and longevity of electrical systems.