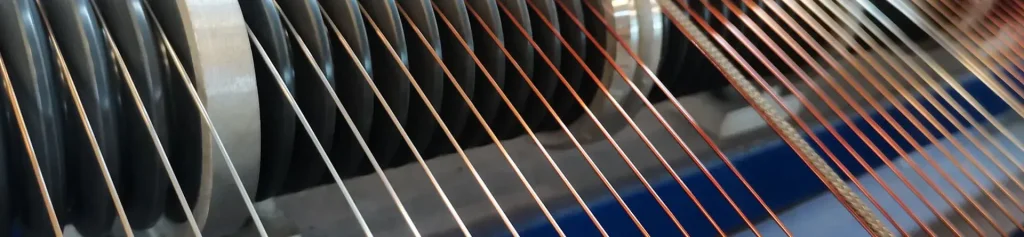
Is Magnet Wire Solid Or Stranded?
To answer this question, we must first introduce electromagnetic wires. Electromagnetic wire or enameled wire is a type of copper or aluminum wire coated with a very thin insulating layer. Electromagnetic wires are used in transformers, inductors, motors, loudspeakers, hard disk head actuators, potentiometers, electromagnets, and other applications that require tight coils. Aluminum is less conductive than copper, so aluminum wires need a larger cross section to compensate. Therefore, copper wire is more energy efficient. But aluminum has the advantage of low cost. Solid and stranded wires are often used in electrical equipment, such as cable assemblies and wire harnesses. A solid wire consists of a solid core, while a stranded wire consists of several strands of thinner wires. Each approach has the unique advantage of making the right choice for the application based on specific project details. Some factors that may affect the choice between stranded and solid wire include: amperage load, use case, cost, metal type, and wire gauge.
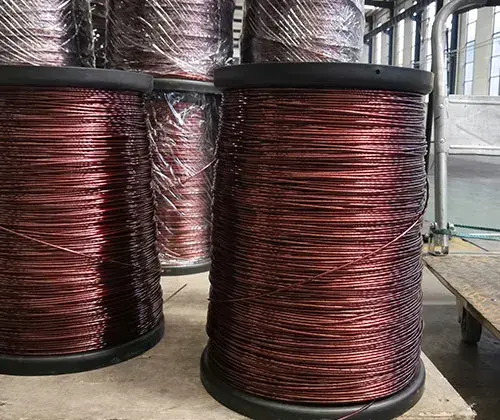
Stranded wire is a thin bundle of wires compressed and insulated by a non-conductive material. Stranded wires are more flexible and are ideal for connecting electronic components in narrow Spaces, or twisting and bending to fit complex geometry. Stranded wire is more flexible and malleable than solid wire, and will not split or cut. It is commonly used in indoor applications, such as electronic devices, circuit boards and speaker wires. Solid metal core wire is a heavier and thicker product than stranded wire. It is ideal for outdoor use where higher durability and higher current are required. This sturdy, low-cost wire is resistant to weather, extreme environmental conditions and frequent movement. It is commonly used to carry high currents throughout building infrastructure, vehicle controls and a variety of outdoor applications.
Comparing stranded wire with solid wire involves exploring the advantages and disadvantages of two very different types of wire. The comparison Narrows the selection based on specific wire characteristics in relation to their intended use and project requirements. You must first determine the application’s requirements for weatherability, flexibility, and resistance to splitting or cutting. Then, choose the wire that best meets those needs. Some of the main differences between stranded and solid copper wire include: stranded and solid wire current capacity. Solid lines are thicker, which means less surface area to dissipate. Thinner wires in stranded wires contain air gaps and larger surface areas, which, together with a single stranded wire, translate into more dissipation. When choosing solid or stranded wire for house wiring, solid wire provides a higher current capacity. Routing. Twisted wire has excellent bending and flexibility, making it easier to bypass obstacles than solid wire. Flexibility. Stranded wire is more flexible and can withstand more vibration and bending without breaking. In applications with significant movement or vibration, solid wires may need to be replaced more frequently than stranded wires. The cost. Solid wire is much cheaper to produce than stranded wire, making it a more affordable option. Make it difficult. The single-core nature of solid wires makes them easier to manufacture. Stranding requires a more complex manufacturing process to hold the thinner wires together. Conductive distance. For longer runs, solid lines are a better choice because they have less current dissipation. The stranded line performs well over short distances. Comparison of advantages. There is no clear choice when it comes to stranded versus solid wire. Each option has distinct advantages under certain circumstances.