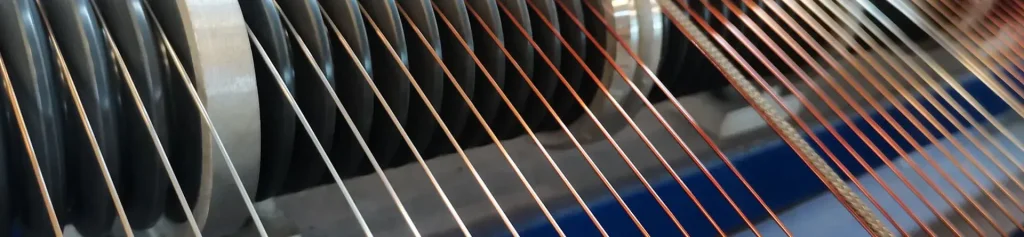
Monitoring and Controlling Viscosity of Wire Enamel in Coating Process
- To safeguard the winding against absorption of moisture
- To resist shock, vibration and mechanical stress by bonding the whole winding, wires and insulation mechanically, into a solid cohesive mass
- To protect the winding against the destructive effects of oil, acid and other chemicals, damp, heat and mould growth and to provide anti-tracking properties
- To improve the electrical properties of the fibrous or other insulators which should remain unimpaired by any of the various destructive influences over a period (for example -the normal cycles of heat and cold resulting from it being switched on and off)
- Coating Quality: Magnet wires must comply with finished product specifications and regulatory requirements, and process control is critical to ensure compliance. Variation in viscosity causes significant change in solvent as well as water-based coating properties affecting printability, fade resistance and drying.
- Coating Uniformity: Inline viscosity monitoring and control can help achieve the required coating quality and reduce coating failures like orange peel, peel off and adhesion failures.
- Reduce coating errors: Viscosity control can help alleviate the frequency of miscues – sticking and picking, twinning, peeling, splitting, cracking, roughness, blistering, bridging and surface erosion.
- Better yield: Ensuring consistency throughout the coating process significantly reduces reject rates saving cost and time. Offline measurement techniques are tedious and unreliable, and involve huge delays in the production process besides incurring high personnel costs to sample and run tests.
- Correct properties: Poor coating quality can adversely affect the desirable properties of the magnet wires – hermetic & burnout resistance, flexibility, mechanical & chemical properties, colouring and market acceptance. All these properties depend on the coating thickness and uniformity, hence controlling viscosity is critical.
- Cost: Coating with incorrect viscosity harms more than just quality. Poor viscosity management drives up usage of pigments and solvents, affecting the profit margins.
- Waste: Materials rejected due to poor quality can be reduced with proper viscosity management.
- Efficiency: Eliminating manual viscosity control frees operators’ time and enables them to focus on other tasks.
- Environment friendly: Lowering the use of pigment and solvent is good for the environment.
- Regulatory compliance: Global and national regulations guide the overall electrical and mechanical properties of the wires. Failure to adhere due to variability in production could lead to significant damages and loss of customers besides liabilities arising from defective workmanship in production process.
Introduction
The global electrical insulation coatings market size in 2015 was USD 2 billion and is expected to grow significantly in the coming years, mainly due to developments in the power sector (global transmission and distribution market). The top emerging market trends facilitating the growth are growing solar power industry, increasing investment in smart grid network and adoption of energy efficient motors. The major application areas are electrical and electronics, automotive, medical and aerospace.
Unstable raw material cost and high costs of formulations are expected to pose a major challenge to market participants. Strict governmental regulations imposed in the market especially in North America and Europe, limit the amount of VOC content in coating products. This has forced the coating manufacturers to go green and adopt sustainability as their agenda, also they are infusing high investments in research and development to develop and innovative and new products which can be offered at low cost, while adhering the regulatory guidelines. Key industry participants in electrical insulation coatings market continue to strive for high integration throughout the value chain, process improvements for superior quality and cost reduction to expand their product portfolio.
Application
Copper and aluminium wires for the manufacture of transformers, electric motors, inductors, generators, speakers, hard disk head actuators, electromagnets, and a wide range of other applications, are coated with a very thin, electrically insulating enamel by dip coating process. Wire coating process is absolutely essential for the following reasons:
Most common wire enamels are Polyvinyl Formal, Polyurethane (PUR), Polyester, Solderable Polyester (PEI), Polyester-imide and Polyimide which behave differently in terms of – adhesion, flexibility, heat shock, solderability, smoothness and speed. The choice of the type of enamelled wire depends on the requirements of the specific application.
The coated wires (also known as magnet wires) are manufactured by applying a coating of enamel to a filament of copper or aluminium conductor in multiple layers. The conductor is passed through a liquid enamel bath or solution of enamel in a solvent and then heated in an oven to drive off the solvent and to cure the enamel; this process is carried out repeatedly for several times depending on the application.
Coating thickness, which depends on the percent solids in the coating solution, is an important design parameter and it is very important to control it within a predetermined range. If the coating solution contains a high percent-solids content, solvent costs can be reduced. The coating thickness is strongly dependent upon viscosity of the liquid enamel or enamel solution and the viscosity of enamel solution must be carefully controlled in order to provide a uniform coatingthickness. When the viscosity fluctuates out of specification, the coat of enamelled wire will be uneven which eventually will lead to poor quality and is often scrapped. Viscosity can have several effects on absorption, colour strength and drying. Highly viscous coating solutions result in tackiness and cause difficulty in transfer onto the substrate, whereas low viscosity makes it more mobile and harder to control and also resulting in increased solvent usage. The viscosity increases when it is not being worked and decreases when there is a constant applied force. The strong correlation between temperature and ink viscosity suggest that fluctuations in temperature can have drastic impact on the viscosity, and thus the coating thickness which is the most crucial parameter.
Why is viscosity monitoring and control critical in wire coating process?
The broad and significant factors which make viscosity management critical in wire coating process are:
To ensure consistent high-quality, uniform coating, the change in viscosity through-out the process stream is monitored in real time, making measurements from a baseline rather than simply measuring absolute values, and making viscosity adjustments by adjusting solvents and compensating for temperature to keep the complete coating process within specified limits.
In order to have a uniform coating and so as not to waste enamel, it is therefore highly desirable that the enamel viscosity be regulated automatically to a substantially constant value. Real-time, in-line viscosity monitoring and control in the coating process is essential to improve performance and reduce costs in almost every wire coating process. Process operators realise the need of a viscometer that monitors viscosity and temperature, and could use temperature-compensated viscosity as the key process variable to ensure consistency and reduce reject rates.