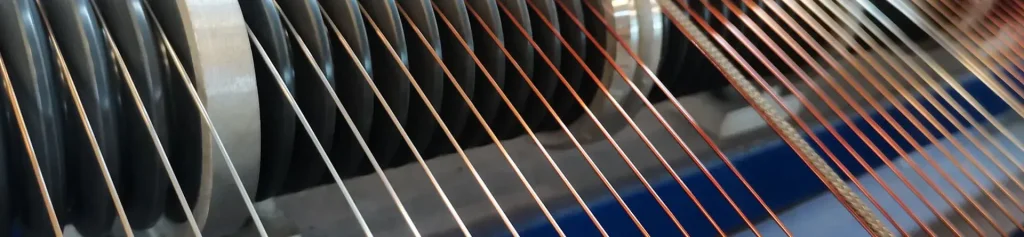
Paint for H Grade Polyurethane Enamelled Wire
The present invention relates to H-grade polyurethane wire enamel which has good pinhole performance of salt water and can be directly welded at low temperature. The H-grade polyurethane wire enamel comprises a hydroxy group contained component, a isocyanate masking component and a solvent, wherein the hydroxy group contained component has the acid value less than 2, the hydroxyl value of 150 to 300 and the number average molecular weight of 1500 to 5000, and at least 1 weight portion of m-phthalic acid, 0.2 to 2 weight portions of terephthalic acid, 0.5 to 3 weight portions of hexanedioic acid and 0.5 to 1.5 weight portions of one type of dihydric alcohol are used as raw materials for synthesing the hydroxy group contained component; the isocyanate masking component is obtained by mixing MDI with polyhydric alcohol, and the polyhydric alcohol comprises at least one types of dihydric alcohol and one types of trihydric alcohol; a paint base has the equivalent ratio of isocyanate group to OH as (0.9 to 1. When reaching the H grade, the wire enamel can form a paint film with good pinhole performance of salt water and the solder-dipping temperature no more than 375 DEG C, so that the H-grade polyurethane wire enamel can satisfy the requirements of miniaturization of motors and electric appliances.
But the saline infusion needle permeability is the H level polyurethane enamelled wire lacquer of cryogenic direct-welding well
Technical field
But the present invention relates to the well H level polyurethane enamelled wire lacquer of cryogenic direct-welding of a kind of saline infusion needle permeability.
Background technology
Mainly (circle line, lenticular wire) bare copper wire, alloy wire and glass yarn are outer in various types of molded lines footpath forms continuous fine and close paint film by the dip-coating mode for wire enamel, make in the winding and produce the good insulation performance layer between the lead and lead, to prevent the circulation of electric current.Polyurethane wire enamel is little with its dielectric loss, have unique excellent properties such as straight weldering, easy dyeing, is widely used in the light current electric products such as accurate coil, motor, instrument, household electrical appliance.Along with the development of electrical industry, the middle and small motor insulating products trends towards high withstand voltage, large vol and miniaturization, and the motor miniaturization causes the raising of working temperature, and the heatproof of polyurethane wire enamel is required also to improve thereupon.In recent years, China’s winding wire increased with average annual 7.6% speed, became the big producing country of world’s winding wire, and output has broken through 300,000 tons of high pointes.But because the winding wire product that China produces is that main file is inferior not high with the B level still, do not satisfy the growth requirement of household electrical appliances and special machines electrical equipment, required relevant insulated wire all needs import.Along with rapid economy development, industries such as automobile, household electrical appliances, to enameled wire resistance toheat and other respective performances as: enameled wire saline infusion needle permeability can and straight weldering performance, also have higher requirement.The saline infusion needle permeability can mainly be to be used to check enameled wire being subjected to external force be forced to the to stretch continuity of back paint film.
By the enameled wire of certain-length is stretched 3%, 5%, 10% respectively, be immersed in the special salt brine solution, two ends apply certain voltage, bubble and red point whether occur by observing conductive line surfaces, thereby judge the successional quality of this enameled wire coat.Above-mentioned saline infusion needle permeability can also can be used for judging enameled wire in use ambient moisture to the influence of enameled wire performance.At present, High-Speed Automatic coiling is all adopted in the coiling of motor and other coil, bring the extension of enameled wire in the winding process inevitably, paint film in the extension process if local fine fisssure or crazing, very likely cause the short circuit phenomenon between lead in actual use, thereby shorten the work-ing life of electrical equipment.This performance is at present as enameled wire and the good and bad primary judging basis of relevant paint.In addition, though polyurethane wire enamel is compared with other wire enamels, has good straight weldering, but, because electrical equipment is tending towards miniaturization at present, the design of insulation system is quite accurate, enameled wire generally all is to carry out scolding tin work after coiling is finished on the corresponding skeleton again, if the too high or scolding tin overlong time of scolding tin temperature all might cause framework deformation, thereby have influence on final assembling, therefore, most of enameled wire users wish that polyurethane wire enamel has lower scolding tin temperature or short scolding tin time, and this helps reducing the generation of substandard products on the one hand, increases work efficiency when carrying out extensive streamline operration on the other hand.
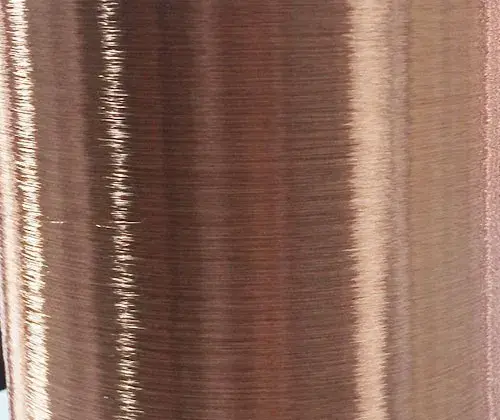
External relevant H level polyurethane enamelled wire lacquer patent as: US4997891 adopts trimellitic acid 1,2-anhydride and 4,4 ‘-‘-diphenylmethane diisocyanate reaction formation imide group, introduce heat-resisting plug gram composition again on molecular structure, heat is 200 ℃ towards temperature, and 400 ℃ are warded off the tin time is 3~4s; The polyurethane wire enamel of US6512073 has the polyamides urea structure, and 390 ℃ are warded off the tin time is 4~5s; The polyurethane wire enamel of US4853261 has the uride structure, and 420 ℃ are warded off the tin time is 1.5s, heat towards temperature greater than 240 ℃.Though its basic index of above-mentioned patent can satisfy the service requirements of H level polyurethane enamelled wire lacquer, has all that to ward off Xi Wendu too high or ward off long deficiency of tin time, and also do not mention the detection data of associated salts liquid drugs injection permeability energy aspect.Domestic relevant H level polyurethane enamelled wire lacquer patent, application number is 02137958.0, the wire enamel that this patent provided is made up of hydroxy component, blocked isocyanate component and solvent three parts.Vibrin as hydroxy component is earlier synthetic terephthalic acid dibasic alcohol or amide imide dibasic alcohol, be polymerized with polyprotonic acid and polyvalent alcohol again, the final index instability of work in-process terephthalic acid dibasic alcohol or amide imide dibasic alcohol, influential to next step reaction; Adopting dimethyl formamide (DMF) in the blocked isocyanate component is synthetic is solvent, and this solvent is easy and aromatic diisocyanate TDI and MDI reaction formation by product in blocked isocyanate component building-up process, is difficult to realize the structure of formulating of recipe; In addition, detect data from the disclosed enameled wire of this patent, line directly relatively, the film thickness that is coated with has belonged to super paste paint film, adopt the existing formed super paste paint film of polyurethane wire enamel all to have good resistance to salt water pin hole, therefore, it reached saline infusion needle permeability can be able to not show it is this specific character that polyurethane wire enamel itself that this patent application provides is had.
From:CNB2004100415858A