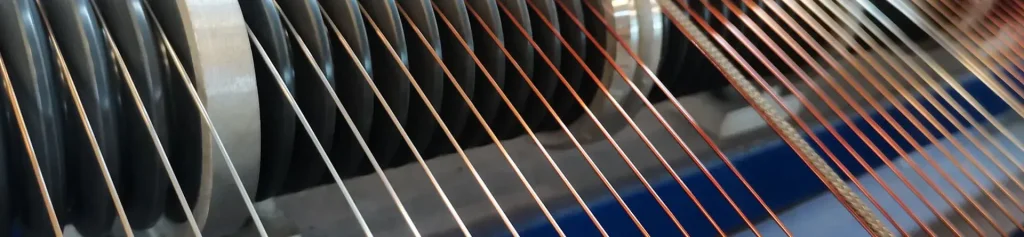
Polyesters from Terephthalic Acid, Ethylene Glycol and a Higher Polyfunctional Alcohol
Polycondensates having carboxylic or carbonic ester groups in the main chain containing cyclic groups containing aromatic groups derived from aromatic dicarboxylic acids and dialcohols from aromatic dicarboxylic acids and dialcohols in combination with polycarboxylic acids and/or polyhydroxy compounds which are at least trifunctionalPolycondensates having carboxylic or carbonic ester groups in the main chain containing cyclic groups containing aromatic groups derived from aromatic dicarboxylic acids and dialcohols from aromatic dicarboxylic acids and dialcohols in combination with polycarboxylic acids and/or polyhydroxy compounds which are at least trifunctional.
This invention relates to synthetic polyester resin and electrical conductors coatedtherewith. More particularly, this invention relates to synthetic polyester resins comprising the product of reaction of (1) a lower dialkyl ester of a member selected from the class consisting of terephthalic acid and isophthalic acid and mixtures of said members, (2) ethylene glycol, and (3) asa-turated aliphatic polyhydric alcohol having at least three hydroxyl groups.
Imus: past, many attempts have been made to .prepare *synthetic’ ‘resins suitable for use as electrical insulat ing material, particularly material which ‘is satisfactory for use as slot insulation in dynamoelectric machines and for use as insulation for conductors which are to’be employed as magnet wires (insulated electrical conductors) in electrical apparatus. It is well known that insulating material which is to be employed for these purposes must beable towithstand extremes of mechanical, chemical, electrical and thermal stresses. Thus, wires to be employed as coil windings in electrical apparatus are generally assembled on automatic or semi-automatic coil winding machines which, by their very nature, bend, twist, stretch and compress the enameled wire in their operation After the coils are wound, it is common practice to coatthem with a varnish solution containing solvents such as ketones, alcohols, phenols and substituted phenols, aliphatic and aromatic hydrocarbons, halogenated carbon compounds, etc. Magnet wire insulation In order to conserve space in electrical apparatus, it isessential that the individual turns which make up the coils be maintained in close proximity to each other. Because ofthe closeness of the turns and the fact that there may be a’largepotentialgradientlbetween adjacent turns, it is necessary that the resins-employed as wire enamels have a high dielectrio strength to -prevent short circuiting between adjacent coils. In operation of electricalapparatus containing ‘coiled Wires, high temperatures are often encountered and the enamels must beable to withstand these high temperatures as well as the mechanical stresses and vibrations encountered in electrical apparatus so that the enamel coatingdoes not soften or come off the wire.
It is well known that the power output of motors and generators can be increased a great deal by increasing the current density in the magnet wires of these machines. However, it has not been practical in the past to increase the current density through magnet wires to the extent desired “because-of the attendant rise in the operating temperature of the magnet wires caused by the increased current. This increased temperature’has meant that conventional organic enamels, which have been relatively economical, could not be used in high current density windings because’the higher operating-temperatures encountered caused’ decomposition of the enamel. -One method of allowing increased current densities-in magnet windings has been to use so-ealled-class B insulation on the magnet wires. This class B insulation ismostly 2,936,296 Patented May 10, 1960 inorganic in nature and comprises an inorganic fibrous material such asasbestos or glass fibers with an inorganic binder or an organic binder holding the inorganic fibers together. Class B insulated magnet wires has been found to be deficien-t in magnet wire applications since its resistance to abrasion is solow that ithas been impossible to fabricate coilsof class B magnet Wire on automatic wire winding machines without tearing and shredding the insulation with the subsequent short circuiting of the coils in use. Another drawback to class B insulated magnet wires is that the insulation tends to be bulky so that it is impossible toplace the wires as closetogether as’ organic film-insulatedwires. Since class B insulated wires require hand manipulation, it has been found that the cost per unittpower output in a class B insulated motor is higher than the corresponding cost per unit power output in a motor .using conventional organic coated wires even though the class B insulated product may have a higherpower output per unit of conductor cross section.
In the past, many attempts have been made to prepare magnet wires which meet all of the mechanical, chemical, electrical and thermal requirements of high temperature magnet wire while still being economically feasible. Cost per unit .power output of a resulting dynamoelectric machine is avery important factor in any magnet wire insulation since an excessive magnet wire cost tends to make amagnet wire. impractical for use regardless of its properties. Excessive cost of a magnet .wireis generally the result of one of the following five factors. The first, and the most obvious, factor is the cost oflthe raw materials .in the resin which is .to’be applied to the conductor. The second cost factoris related to the ability ofthe’resinous material to be’dissolved in readily available, inexpensive solvents. Since resinous materials are preferably stdred’and transported in solution, the bulk and weight of the solvent play a large part’in the cost of having theresin at the placezwhere it is to be used at the time an to be used; Inpractice, it has been found that is desirable to employ’ resinous materials as wire enamels whichare capable of being held in solutions which contain :at least 30m 50 percent, by weight, of solids. Since gthe solvents in the resinous solution are generally allowed-to escape without recovery from the wire coating-apparatus, the cost of the solvent is an “important facto’r in the costof the cured enamel. The third factor which vitally atfects the cost of an enameled wire is thetime required to cure the enamel once it has been} applied to the conductor. If this time is excessive, anunduly large baking oven is required or the speed of the wire through the oven must be maintained at an uneconomically low rate. The fourth factor which vitally affects the cost of a magnet wire is the flexibility of lthe conditions which may be employed in applying the resin to the conductors and in curing the resin once it has been applied. If the Wire speed range in the curing operation, the curing temperature, and the wire diameter sizes are critical, it is obvious that a large amount ofdefective magnet wire may be prepared under mass production conditions, whereas, if large variations in curing conditions-are allowable, only a very small amount of the magnet wire prepared need be discarded because of defective insulation. The fifth factor which is important in the cost of a magnet Wire is the ability of the same resinous solutionto be applied to “both round and-rectang’ularconductors and to conductors made of various metals. If different resin solutions must be used for –each type-of-conductor, the time required to changethe resin solution isan integral part of the magnet wire cost.
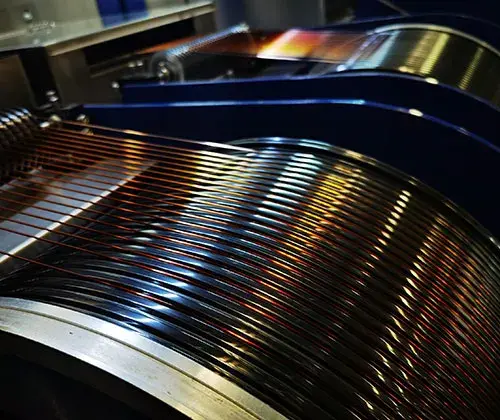
In order to determine whether the insulation on a magnet wirewill withstand the mechanical, chemical, electrical and thermal stresses encountered in winding machines and electrical apparatus, it is customary to apply the resin to a conductor by a method which will be described hereinafter and to subject the enameled wire to a series of tests which have been designed to measure the various properties of the enamel on the wire. These tests, which will be described in detail later, include the abrasion resistance test, the 25 percent elongation plus 3X flexibility test, the 70-30 solvent resistance test, the 50-50 solvent resistance test, the dielectric strength tests, the elongation after heat aging test, the heat shock test, the cut-through temperature test, the high temperature weight loss test, and the high temperature dielectric strength loss test.
We have found that the enamel on a conductor which will Withstand the mechanical, chemical and electrical stresses encountered in magnet wire applications and which is operable at temperatures ofat least 135 C. for extended periods of time must withstand at least 30 strokes in the abrasionresistance test, must pass the 25 percent elongation plus 3X flexibility test, must show no attack on the insulation in either of the solvent resistance tests, must have a dielectric strength of at least 2000 volts per mil, mercury immersion, twisted pair, or aluminum foil. In addition, this insulated conductor must show no insulation defects when elongated 15 percent after heat aging for 100 hours at 185 C. or when elongated 9 percent after heat aging for 24 hours at 225 C., must show no insulation defects in windings having a diameter more than five times the diameter of the conductor when wound on a conical mandrel having an apex angle of about 20 degrees in the heat shock test, must have a cut-through temperature greater than 175 C., must show less than a 3 percent insulation weight loss when heated in a sealed tube for 1000 hours at 200 C., and must not show a loss in dielectric strength of more than 70 percent after heat aging in 25 percent relative humidity air for 500 hours at 200 C.
From: US474624A events