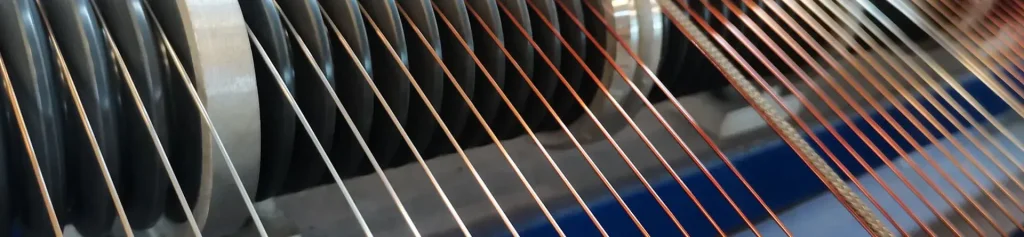
Polyurethane Enameled Wire
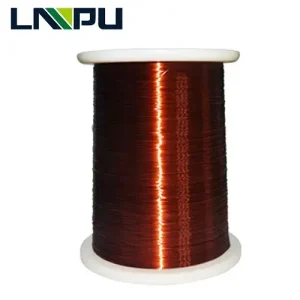
What is Polyurethane Enameled Wire?
Polyurethane enameled wire, often known as magnet wire, is a type of insulated wire used in the construction of coils and windings in electrical applications. The polyester composition of polyurethane enamels is composed of dimethyl terephthalate, glycol and glyceride. The other components are composed of contains light base resin, diisocyanate and various additives.
Polyurethane enameled wire consists of copper wire and polyester resin. It can work stably in 240 ° C environment, while the paint material can be used safely under 350 ° C environment.
Heat Resistance Grades:
130°C (B Class), 155°C (F Level), 180°C (H Level)
Diameter Range:
0.010mm – 6.00mm
Characteristics of Polyurethane Enameled Wire
Self-solderable: Some types of polyurethane enameled wire can be soldered without stripping the insulation, as it melts away during soldering.
High Dielectric Strength: Ensures effective insulation even at high voltages.
Thin Insulation: Allows for compact winding designs, saving space and material.
Polyurethane enameled wire, with its low dielectric loss, dyeing, high speed and has good mechanical strength and resistance to scratches, paint film adhesion performance, good conductivity, chemical resistance, thermal stability and solvent resistance, straight welding and excellent performance
Types of Polyurethane Enameled Wire
Single Coated: A single layer of polyurethane insulation. Suitable for applications where space and weight are critical factors.
Double Coated: An additional layer of insulation over the first, offering enhanced protection and thermal resistance.
Self-bonding: These wires have a layer of thermoplastic bonding agent, allowing coils to be formed without the need for impregnation.
Applications
Transformers: Used in the windings of transformers for efficient energy transfer.
Motors: Integral in the construction of motor windings, including both AC and DC motors.
Generators: Used in the winding of generators for converting mechanical energy into electrical energy.
Inductors and Chokes: Essential for creating inductors and chokes which are used in various electronic circuits.
Relays and Solenoids: Used in the coils of relays and solenoids for creating electromagnetic fields.
Precision winding, instruments, household appliances, etc. In the low voltage electrical appliances.