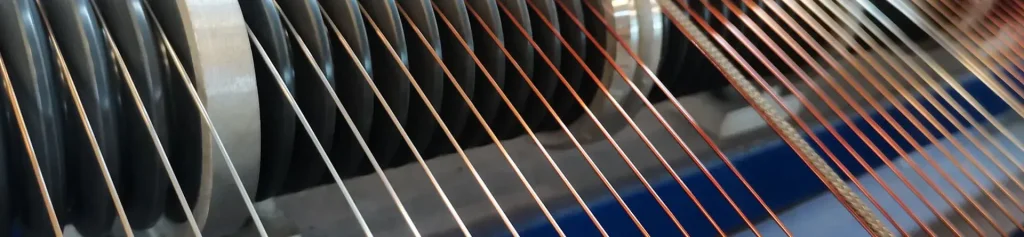
Polyurethane Magnet Wire UEW QA
The polyurethane enameled wire is widely used in low-voltage electrical products such as precision coils, motors, meters, household appliances, etc. due to its excellent properties such as low dielectric loss, easy dyeing, high coating rate, and direct solderability. The direct solderability of polyurethane enameled wire means that the enameled wire coated with paint film is in the tin enamel tank. The ability to put on the tin. In this way, when the polyurethane enameled wire needs a joint, it is not necessary to remove the coating in advance. Its direct solderability feature simplifies the production process of the winding wire and effectively improves the production efficiency.
HS code for polyurethane enameled copper/aluminum wire: 85441190
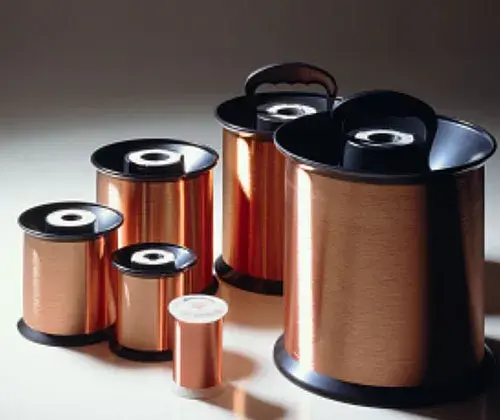
How to solder enameled wire? How to solder enameled copper wire?
Polyurethane enameled wire has received more and more attention because of its direct solderability. In recent years, its market share has been expanding and it has a good application prospect. The polyester component used in the traditional polyurethane enameled wire lacquer is formed by the esterification condensation polymerization of dimethyl terephthalate, ethylene glycol and glycerol. This traditional process has the disadvantages of complex process, high cost, and large environmental pollution. At the same time, the polyurethane paint prepared has low heat resistance and poor heat and humidity resistance. Therefore, there are some reports at home and abroad that have proposed the modification research approach of polyurethane enameled wire paint, but a reasonable process plan has not been proposed in terms of comprehensive optimization of heat resistance grade, comprehensive performance, process and cost and other influencing factors.
Thermal Class | Insulation building | China’s sign | International sign | Characteristics | Useful |
130 | Heavy | QA-2/130 | 2UEW/130 | 1. Easy to color, high frequency performance 2. Self-soldering, don’t remove the enamel 3. High baud performance 4. The heat resistance is superior to that of acetal enameled wire (PV>60) 5. No salt water pinhole 6. Suitable for high-speed winding |
1. Winding of communication devices 2. Coil for computerized machine 3. Intermediate frequency and high frequency coil 4. Suitable for enameled stranded wire 5. Various relays and inductance coils |
Thin | QA-1/130 | 1UEW/130 | |||
155 | Heavy | QA-2/155 | 2UEW/155 | ||
Thin | QA-1/155 | 1UEW/155 | |||
180 | Heavy | QA-2/180 | 2UEW/180 | ||
Thin | QA-1/180 | 1UEW/180 |
Factors Affecting the Direct Weldability of Polyurethane Enameled Wire
The main factors affecting the direct weldability of polyurethane enameled wire are:
(1) Side reactions and catalysts;
(2) The structure and ratio of the base resin;
(3) Baking process of enameled wire.
Types of polyurethane enameled wire
enameled copper wire
enameled aluminum wire
HS code for polyurethane enameled wire 85441190
Catalyst of Polyurethane enameled wire
Type of catalyst: The common reactions of polyurethane enameled wire paint include the addition and sealing reaction of isocyanate, the synthesis reaction of light-based resin components, the curing reaction of the varnish liquid on the winding wire after the paint is mixed, and the enameled wire in the enamel. Decomposition reaction in the tin bath. The choice of catalyst is also embodied in these aspects.
There are three commonly used catalysts: tertiary amines, metal compounds and organic compounds. The application experience related to polyurethane enameled wire paint mainly has the following points: A tin catalyst may be stronger than tertiary amines for NCO/OH type reaction. B. In the process of manufacturing polyurethane prepolymers, a small amount of tin catalysts can effectively guide the reaction of isocyanate groups and light groups to form linear amino compounds; tertiary amine catalysts are easy to cause branching reactions and cause resins The viscosity is too high or gelled. C acidic conditions are beneficial to the reaction of isocyanate groups and light groups to form urethanes. Under alkaline conditions, while the reaction of isocyanate groups and light groups is accelerated, other side reactions are also accelerated. D. Choose a catalyst suitable for catalyzing the addition reaction of isocyanate groups, which should also be determined in conjunction with the actual tin enamel experiment of the winding wire. Although some catalysts show excellent catalytic selectivity in the addition reaction of isocyanate groups, after the tin enamel test, it is found that more residues are left and the soldering time is prolonged. E. The specific situation needs specific treatment. In the actual production of coatings, a series of actual tests should be used to determine the appropriate catalyst species.
For the choice of catalyst used in polyurethane enamelled wire paint, since the reaction of isocyanate groups is very complicated, the effect of different substituents on the _L isocyanate group on the electronegativity of the isocyanate group, the same catalyst It can show different effects on isocyanates containing different substituents. In addition, the steric hindrance of the molecular structure of the catalyst and the reactant should also be given enough attention when selecting the catalyst.
The amount of catalyst: After selecting the appropriate type of catalyst, the definition of the amount is mainly based on two aspects: the storage period of the paint and the curing requirements of the enameling process. In general, the shelf life of the paint solution is inversely proportional to the amount of catalyst. The higher the amount of catalyst, the shelf life of the paint solution is relatively short. The author also found in the laboratory that some catalysts not only affect the storage period, but may also cause discoloration of some varnishes.
The impact of the catalyst on the enameled process is mainly due to the continuous improvement and change of the enameled process. Under the premise of ensuring the excellent performance of the enameled wire, the coating rate of the enameled wire is getting faster and faster, and the corresponding curing rate of the paint solution is also required to be increased at the same time. Of course, we can solve it by increasing the amount of catalyst, but it also brings problems such as the storage stability of the paint solution.
The influence of base resin structure and ratio on polyurethane enameled wire
Polyurethane wire enamel is composed of light-based resin, isocyanate sealant and various additives.
The influence of the structure of the base resin on the solderability: an ideal base resin structure is the basis for ensuring the excellent performance of the enameled wire. Different enameled wires have different requirements for enameled wires. In addition to direct solderability, polyurethane enameled wire also has strict requirements on the salt water pinhole resistance (ie, the continuity of the paint film) of the wire.
The influence of the structure of the base resin on the direct solderability can be considered from two aspects: the degree of branching of the resin and the molecular structure. Tests have proved that reducing the degree of branching of the base resin has a certain effect on improving the direct welding performance of the paint film. However, this adjustment method, the paint film actually cured on the winding wire, is often due to the decrease in crosslink density Bringing the reduction of the salt water pinhole resistance of the winding wire; good curing of the paint film and sufficient crosslinking density can ensure the salt water pinhole resistance of the enameled wire. However, the excessively high crosslinking density has caused the direct welding performance of the winding wire. decline. Therefore, the appropriate paint film cross-linking density should be controlled by adjusting the structure of the base resin to achieve a balance between the direct-welding performance and the salt-water-resistant pinhole performance of the winding wire.
The molecular structure of the base resin mainly refers to several factors such as the type and number of heat-resistant groups in the molecular structure, the steric hindrance effect of the molecular structure and the molecular activation energy. A sufficient content of heat-resistant groups in the molecular structure can ensure the thermal shock performance of the winding wire, but an excessively high content will cause a decrease in the direct welding performance; a molecular structure with a large steric hindrance will also affect the heat of the urethane bond in the paint film. Decomposition; if the activation energy of the organic molecules in the tin bath after the paint film is cured is too high, it will also affect the direct welding performance of the winding wire.
In order to obtain practically usable resin containing light base material, after a reasonable theoretical formula is determined, the influence of the control of the base material resin production process on the properties of the final synthetic resin cannot be ignored. The control method used in the actual production process is mainly to control the alcohol loss during the synthesis process and the temperature and time of the acylation reaction. The author once found in the factory that the same formula, due to the lack of understanding of the new equipment, the actual operation of the production workers’ control deviations, resulting in different batches of resins in terms of heating time and viscosity compared with the normal base resin. The varnish made from this resin has a large difference in performance and appearance after coating on the winding wire, and the tin enamelling time is prolonged.
The influence of the proportion on the direct welding performance: the proportion reaction of the base resin is a problem of the ratio of NCO to OH in the molecular structure. When the paint solution is in the baking oven, the sealing resin undergoes a deblocking reaction, and the deblocked isocyanate groups react with the light-based resin to form a film through cross-linking.
The reaction of isocyanato groups is very complicated, and different ratios of one NCO to OH will bring about different paint film properties. If the ratio is too high, the branching reaction during the curing process of the paint film will increase, causing the crosslinking density of the paint film to be too large, which will affect the direct welding performance of the enameled wire; if the ratio is too low, the crosslinking density of the paint film will be low, and the resistance of the paint film will be low. The saline pinhole performance cannot meet the requirements of actual use. A suitable ratio of one NCO/one OH can provide a relatively ideal crosslinking density for the paint film. Of course, when the enameled wire is required to have high salt water resistance and pinhole resistance, but the direct welding performance is relatively low, we can appropriately lower this ratio.
The effect of baking process on polyurethane enameled wire
Under-baked enameled wire cannot guarantee the excellent performance of the paint film. The over-baked polyurethane enameled wire will have a decline in its direct soldering performance. This is mainly due to the reaction between the isocyanate group and the amino acid bond or itself during the baking process of the paint, which causes the content of the amino acid bond in the cured paint film to decrease, thereby affecting the direct solderability of the paint film.
Difference between enamel and polyurethane of magnet wire
Polynitrogen is a type of enamel used for enameled wire. It has excellent electrical insulation and direct solderability (that is, the performance of soldering directly without removing the paint film).