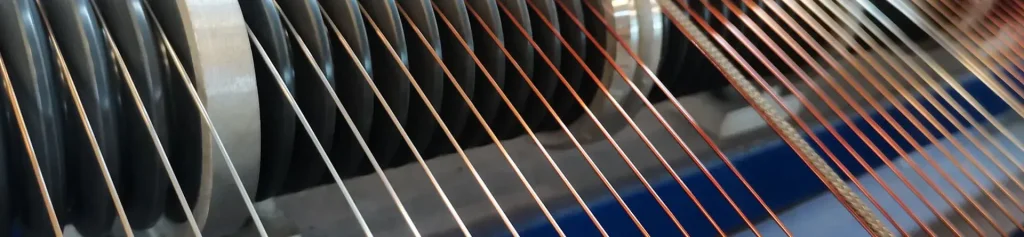
Questions and Answers About Enameled Wire
Q: What’s the difference between an enameled aluminum wire and an enameled copper wire?
A: Copper is more conductive, requiring smaller cross-section for a given current and easier to solder or otherwise connect.
Aluminum is less conductive, requiring larger cross-section for a given current. Despite this, it is cheaper than copper.
Q: Can a copper wire be repaired with an aluminum wire?
A: No. It can be replaced, but not spliced together. And aluminum is (today) contraindicated for electrical wiring.
Q: Can I use 3 * 17 SWG enamel wire instead of 8 SWG which has the same diameter (4 mm)? Will the same ampere flow?
A: In wires the cross section area is the important factor, not the diameter; the cross section area is proportional to the square of the radius or diameter.
So three wires having one third the diameter will have only 1/9th the cross section and will be unable to carry the same current without larger voltage drop and heat loss due to 9x higher resistance.
My quick foray into British standard gauge says 17 SWG is .056 inches (1.42 mm) dia and 8 SWG is .160 inches (4.06 mm) dia.
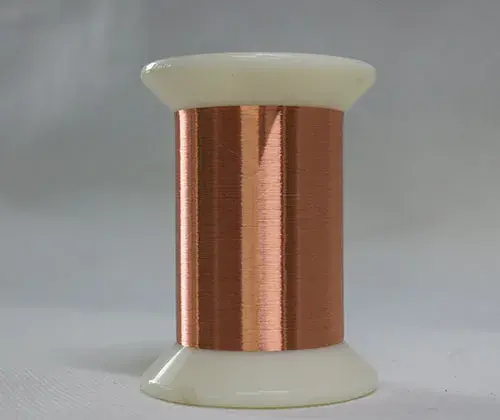
Q: What is more preferable in making solenoid, a pure copper wire or an enameled copper wire?
A: The wire has to be insulated, so enameled copper wire is your only practical choice. You could use other insulated wire, but you cannot get the same number of turns in a given space with that as you could with enameled wire (known as “magnet wire”) because its insulation is very thin.
Q: How to solder aluminum to copper?
A: Thoroughly remove oil stains, dirt, insulating layers, etc. on the base metal before welding; heat the base metal first, heat the thick parts first, then heat the thin parts; heat the copper parts first, then heat the aluminum parts; move the welding torch back and forth to heat and weld When the temperature of the weldment reaches 450-500°C, add the welding wire to the welding part to let the welding wire melt evenly and flow into the weld (do not use the flame to directly heat the welding wire, the welding wire mainly depends on the temperature of the base metal to melt).
Q: Can I use non enameled copper wire in crystal radio?
A: Definitely – but there are different kinds of insulation on “magnet wire” (the thin solid copper wire used to wind coils). The old style is enamel, which has to be scraped off in order to allow soldering, but now there is urethane insulation, which will melt when molten solder touches it.
You can make a blob of molten solder on the iron tip and poke the end of the wire into it. After a few seconds the wire will be coated with solder when you pull it out.
In the days before ferrites you would wind enamel wire around a cylindrical object like a cardboard oatmeal cannister (this may no longer be available). Trial and error would produce a coil that would display a self-resonant point in the AM broadcast band (the lower end is at 530 KHz).
You could slide a contact across the coil (where the insulation had been scraped off) and the resonance would increase as the number of turns decreased. You can connect a pair of high-impedance earphones (crystal or 2000 ohm magnetic) to the coil through a signal diode (1N34 takes less voltage because it’s germanium, but silicon diodes like 1N914/1N4148) would also work). It’s a good idea to have a capacitor of about 1 nF (.001 uF) across the earphones.
Q: Which is bigger, copper wire or aluminum wire?
A: Both can be made into a wire of the same exact thickness (size, or gauge), but if they’re the same thickness they’ll have different levels of conductivity.
Q:Why are both aluminum and copper can be used in electrical wires?
A: Engineering is a practice of tradeoffs, and depending on the circumstances and priorities either copper or aluminum can be preferable for a given application.
Copper has higher conductivity, but is heavier and is (currently) a fair bit more expensive.
Aluminum is less expensive and lighter weight, and cheaper, but its oxidation behavior means that special precautions must be taken at connection points.
Copper is used in most household and small-gauge wiring, because it’s easier to work with and the ratio between material cost and labor cost is low.
Aluminum is used for large-gauge transmission wires, because the ratio between material cost and labor cost is high, and work will be performed by specially-trained linemen; it is also used for small-gauge wiring in airplanes because that application is extremely sensitive to weight.
Q: What are the disadvantages of using aluminium wire instead of copper wire?
A: Aluminum conductor has a quality that some call “cold flow”. One can tighten the conductor in terminals, and it will work satisfactorily – for a while. After an extended period of time, the shape of the conductor under the securing device will not be the same as it was originally. Unless someone, as a maintenance activity, periodically inspects terminals and tightens them back to “snug”, the union between conductor and terminal may experience an arc. Taken to the extreme, a fire could result. Not a desirable situation. Most residential installations don’t have someone to go around periodically and tighten, or “snug up”, all the aluminum conductor connections.
Commercial and industrial manufacturing operations – especially those that manufacture aluminum products – have a maintenance staff to inspect all the terminations as part of their scheduled maintenance programs. Larger conductors in copper are expensive, therefore many activities avoid the expense and use aluminum conductors for larger current rating applications. They are accustomed to dealing with the AL conductor qualities.
Q: What is an enameled wire used for?
A: Enameled wire is used to wind electromagnets, coils for transformers, choke coils and other inductors.