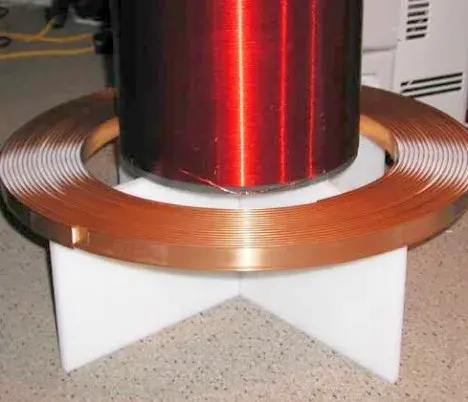
Strap-copper coils with paper or other insulating material between turns merely require a strongtension and some hammering with a rawhide mallet or a piece of wood interposed between the coil and the hammer in order to cause the insulated strap or ribon of copper to lie properly in place. The insulation should be suficiently strong, mechanically, to withstand such treatment. In one form of winding machine, a roll of strap copper and a roll of strip paper, about double the width of the strap copper, are fed through a folding device after they leave their respective rolls in such a manner that the paper is folded longitudinally around the copper as the coil is being wound.