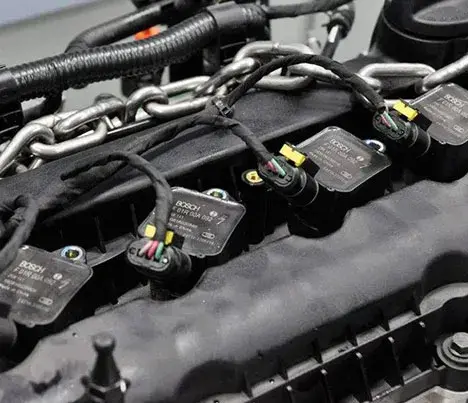
Magnet Coils in the case of Electric Vehicle
Electric vehicles are being favored by manufacturers as a means of transportation driven by new energy sources. The amazing fact is that electric vehicle have a much longer history than fuel vehicle. The first oil-fired generator to serve as the heart of a conventional car was successfully worked in 1885, while the first electric car appeared in 1839. With the development of automobile, the traditional fuel engine can not meet the purpose of low emission and consumption gradually. The advantages of Conductor coil as the power device of electric energy are constantly amplified. Getting rid of fuel is the biggest advantage that it shows, saving the earth’s non-renewable resources and reducing carbon dioxide emissions. The core part of the electric device is composed of the stator and rotor. Usually, there are two groups of enameled copper wires inside the coils as conductors. The main wires are made by 0.5-1mm enameled copper wire wound with 200-500 turns, and the finer secondary enameled wires are made of 0.1mm wire wound with 15,000-25,000 turns. According to the power supply can be divided into alternating current motor and direct current motor two. These magnet coils are divided into five types: 120 (grade E), 180 (grade H), 200 (grade C), 220 (grade C Plus) and 240 (grade HC) to meet different operating temperatures.