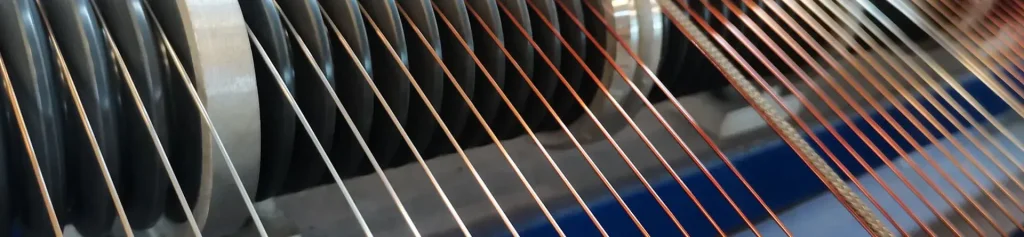
The Crucial Role of Enamelled Wire in Precision Instruments
Precision instruments are the backbone of various industries, from healthcare and aerospace to telecommunications and electronics. These devices demand meticulous engineering and utmost accuracy in their construction. One often-overlooked component that plays a pivotal role in these instruments is enamelled wire. In this blog, we will delve into the fascinating world of enamelled wire and how it is used in precision instruments.
What is Enamelled Wire?
Enamelled wire, also known as magnet wire or winding wire, is a type of electrical conductor that is insulated with a thin layer of enamel (usually made of polyester, polyurethane, or polyimide). This enamel insulation provides electrical insulation and thermal protection, allowing the wire to be wound tightly without short-circuiting.
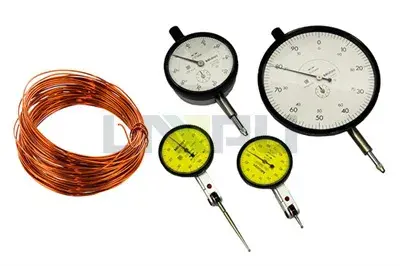
Applications in Precision Instruments
Transformers and Inductors: Enamelled wire is extensively used in transformers and inductors found in precision instruments. The precise winding of enamelled wire ensures efficient energy transfer and minimal energy loss. This is crucial for maintaining the accuracy and reliability of the instrument’s measurements or operations.
Solenoids: Solenoids are electromagnetic devices that convert electrical energy into mechanical motion. Enamelled wire is commonly used in solenoid coils to ensure a precise and consistent magnetic field, which is essential in applications like valve control and positioning systems.
Sensors: Many precision instruments rely on sensors to measure various parameters such as temperature, pressure, and strain. Enamelled wire is employed in the construction of these sensors, ensuring accurate signal transmission without interference.
Coils and Windings: Precision instruments often require custom-designed coils and windings. Enamelled wire is the preferred choice due to its ability to provide tight, uniform windings. These coils are used in devices like gyroscope sensors, magnetic resonance imaging (MRI) machines, and high-frequency oscillators.
Miniaturization: Enamelled wire’s thin insulation layer allows for the creation of compact and lightweight components within precision instruments. As devices become increasingly miniaturized, enamelled wire remains a vital element for ensuring that space is utilized efficiently without compromising performance.
High-Frequency Applications: In instruments that operate at high frequencies, such as oscilloscopes and spectrum analyzers, enamelled wire is indispensable. Its low dielectric loss and ability to handle high-frequency signals make it an ideal choice for maintaining signal integrity.
Advantages of Enamelled Wire in Precision Instruments
Electrical Insulation: Enamelled wire provides excellent electrical insulation, preventing short-circuits and ensuring consistent performance even in high-voltage applications.
Thermal Resistance: The enamel insulation can withstand high temperatures, making enamelled wire suitable for instruments that generate heat during operation.
Precision Winding: Enamelled wire is easy to wind tightly and uniformly, ensuring precision in the construction of coils and windings.
Durability: Enamelled wire is known for its durability and resistance to environmental factors, contributing to the longevity of precision instruments.
Size Reduction: Its thin insulation allows for smaller and more compact designs, a critical consideration in modern precision instrument design.
Enamelled wire might be a humble component, but its role in precision instruments cannot be overstated. From transformers and sensors to coils and solenoids, enamelled wire ensures the reliability, accuracy, and longevity of these critical devices. As technology continues to advance and instruments become even more precise and compact, the importance of enamelled wire is only set to grow. It serves as a testament to the fact that even the smallest components play a monumental role in the world of precision engineering.