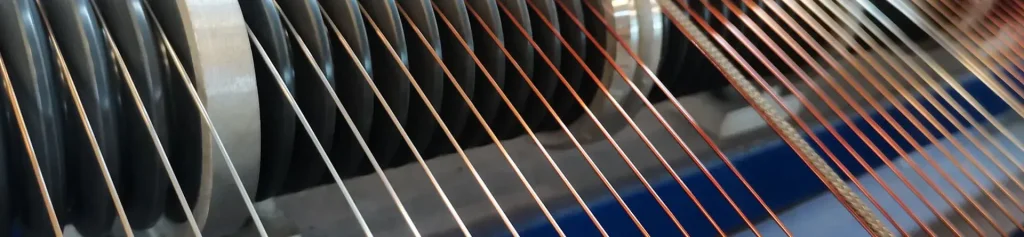
The Impact of Coating Thickness on Wire Properties
Wire coatings play a vital role in protecting and enhancing the performance of wires across various industries. Among the factors that influence a wire’s properties, the thickness of its coating holds significant importance.
Protection against Environmental Factors:
Coatings serve as a protective layer for wires, shielding them from environmental factors such as moisture, chemicals, abrasion, and temperature variations. The thickness of the coating directly affects the wire’s ability to withstand these factors. A thicker coating provides a more robust barrier, enhancing the wire’s resistance to corrosion and mechanical damage. It ensures long-term durability, particularly in harsh operating conditions, and extends the wire’s overall lifespan.
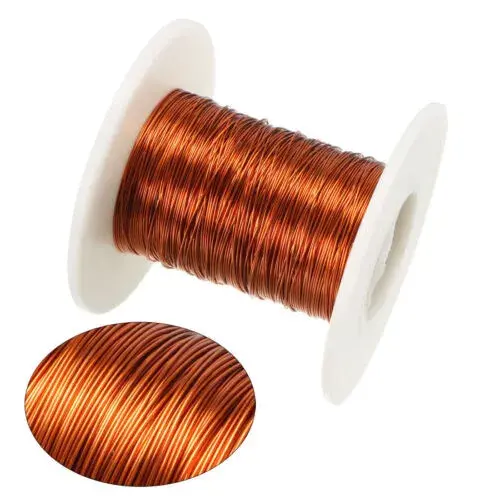
Electrical Insulation:
In electrical applications, wire coatings are crucial for providing insulation and preventing current leakage. The thickness of the coating determines the wire’s insulation properties. A thicker coating offers higher dielectric strength, reducing the risk of electrical breakdown and enhancing safety. It also minimizes the chances of short circuits and electrical interference, ensuring reliable performance in various electrical systems.
Flexibility and Bendability:
The thickness of the wire coating can influence its flexibility and bendability. A thinner coating allows for greater flexibility, making the wire more pliable and easier to handle during installation or routing. This is particularly important in applications where wires need to be routed through tight spaces or around corners. On the other hand, a thicker coating may reduce the wire’s flexibility, requiring careful consideration during design and installation processes.
Thermal Conductivity:
Wire coatings can impact the wire’s thermal conductivity, affecting its ability to dissipate heat. A thinner coating promotes better heat transfer, allowing the wire to dissipate heat more efficiently. This is especially critical in high-temperature environments or applications that generate significant heat, as it helps prevent overheating and ensures optimal performance. Conversely, a thicker coating may impede heat dissipation, potentially leading to temperature buildup and compromising the wire’s functionality.
Weight and Size Considerations:
Coating thickness can have implications for the weight and size of the wire. Thicker coatings add extra material to the wire, increasing its overall weight and potentially impacting applications where weight is a concern, such as aerospace or automotive industries. Moreover, thicker coatings may require larger wire diameters, affecting space constraints in compact designs. Therefore, striking a balance between coating thickness, weight, and size is essential to meet specific application requirements.
Conclusion:
The thickness of wire coatings significantly influences the wire’s properties, including protection against environmental factors, electrical insulation, flexibility, thermal conductivity, and weight considerations. Selecting the appropriate coating thickness is crucial to ensure optimal performance, durability, and safety in various applications. By understanding the effects of coating thickness, manufacturers and engineers can make informed decisions when choosing wire coatings, striking the right balance between functionality, reliability, and design requirements.