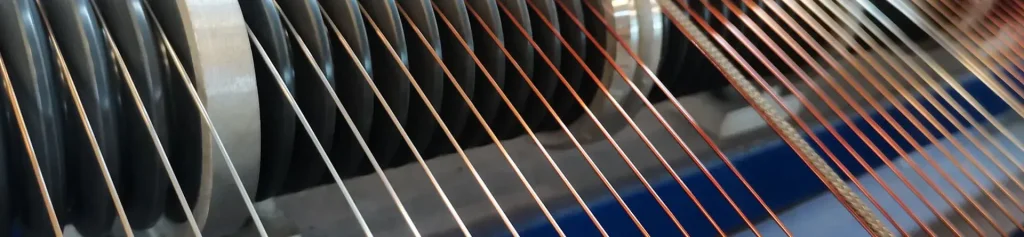
The Relationship Between Standard Performance Of Enameled Wire And Winding Characteristics
Enameled wire performance-size
1. Conductor size
2. Conductor out-of-roundness
3. Insulation thickness
4. Dimensions
5. Thickness of self-adhesive layer of enameled round wire
6. eccentricity


The influence of eccentricity tolerance?
The insulating ability of the paint film is proportional to the thickness. The eccentricity of the paint film is similar to the “barrel principle”, and the actual effective insulating capacity is determined by the thinnest part. If the conductor is not round, under the action of the “skin effect”, the smaller the R angle, the higher the electric field strength, and the thinnest paint film, which becomes a weak point.
The uneven thickness of the paint film results in different degrees of curing, and different stresses will also occur when the force is applied. The paint film is prone to damage during the deformation process such as stretching and bending of the enameled wire, which reduces the workability and reliable insulation. Sex.
In recent years, with the improvement of machining accuracy, the roundness and taper of drawing dies and painting dies have been greatly improved. The high-speed enameling machine has increased the centripetal force of copper wire decomposition in the painting dies, and the effect of “self-centering” Better, to make the distribution of the paint film in the circumferential direction more and more uniform, and the pressure resistance of the enameled wire is getting higher and higher. The first-level film thickness enameled wire produced by the high-speed enameling machine can easily meet the pressure resistance requirements of the second-level film thickness enameled wire, and the CPK value is also higher.
In the traditional design, the motors used in 220V or 380V systems mostly use secondary film thickness enameled wires. In high-efficiency motors, such as IE4 industrial motors and inverter air conditioners, the primary film thickness (thin paint film) is used. . In fact, aside from the existing design, almost all industrial motors can use thin enameled wires that meet the secondary insulation requirements, which will bring great efficiency improvements and resource conservation. (The thinner the paint film, even if the core design is not changed, the slot full rate will decrease and the copper consumption will be greatly reduced)
The smaller the eccentricity, the better the degree of stretch resistance. The tension can be increased during the winding process, so that the windings are tighter and smaller, and the heat dissipation and stability of the windings (reduce the friction between the wires during operation) can be obtained improve.
Enameled wire performance-mechanical performance
1. Elongation at break
2. tensile strength
3. Resilience
4. Flexibility and adhesion
4.1 Round rod winding test
4.2 Tensile test (applicable to enameled round wires with a nominal conductor diameter of 1.600mm or more)
4.3 Quick break test (applicable to enameled round wires with a nominal conductor diameter of 1.000mm and below)
4.4 Peel test (applicable to enameled round wires with a nominal conductor diameter of 1.000mm or more)
5. Scratch resistance (suitable for enameled round wire)
6. Thermal bonding and solvent bonding
7.friction test method
Main indicators of softness

The softness of the enameled wire mainly affects the forming of the winding. The greater the rebound angle, the greater the force to retract the enameled wire after winding. In the manual wire embedding process, the straight section is easy to bulge into an arc, and the end of the wire retracts to an uncertain position, resulting in offline difficult. Among the windings whose ends need to be shaped, the windings with large resilience will have greater stress during shaping, and the insulation will be easily damaged during shaping.
For the annealed wire, the strength of the conductor decreases, it is easy to be broken during the winding process, or there is a serious thinning resistance out of tolerance.
Coefficient of friction
Error factors of static friction coefficient test:
1. The error of line straightening
2. Methods of unloading
3. The position of the sensor head
Test Techniques for Static Friction Coefficient

Advantages of dynamic friction coefficient:
1. Reduce the influence of human factors, and the test results are more reliable;
2. Closer to the actual winding process
Schematic diagram of dynamic friction coefficient test

Enameled wire performance-chemical performance
1. Solvent resistance
*2. Refrigerant resistant
*3, direct solderability
*4, resistance to hydrolysis and transformer oil
Enameled wire performance-electrical performance
1. Resistance
2. Breakdown voltage
3. Paint film continuity (*electric spark test)
4. Dielectric loss coefficient
The effect of defects on windings

Enameled wire performance-thermal performance
1. Thermal shock
2. Soften breakdown
3. Temperature index
*4, weightlessness
*5, high temperature failure test
The practical significance of thermal performance indicators
Thermal shock
【Enameled wire resistance to elastic deformation. 】
The winding changes state frequently between normal temperature and normal operating temperature, and the paint film continuously undergoes elastic deformation under thermal stress conditions. During the life cycle, it is required that the paint film should not experience insulation failure under the corresponding thermal level temperature condition.
Thermal shock is a manifestation of the temperature index of the paint film.
The thermal shock temperature is 20°C higher than the temperature resistance grade of the paint film.

Softening breakdown (thermoplastic flow)
【Enameled wire has the ability to resist heat-resistant plastic deformation. 】
The tension during winding, the centrifugal force during motor operation and the squeezing force caused by vibration may all act on the motor winding individually or together. In the event of a sudden and rapid temperature rise (such as motor stalling), the paint film will undergo thermoplastic deformation Will not cause the ability of turn-to-turn breakdown.

In the IEC standard, the 200-class enameled wire requires that two enameled wires that intersect vertically under the condition of 320℃, and a certain load is applied at the intersection point, and there should be no breakdown within 2 minutes. Theoretically, the motor made of 200-class enameled wire will not break down the insulation within 2 minutes when the rotor is blocked and the temperature is increased to 320°C. For example, if a child continues to press the switch after the window motor is in place, the electric vehicle has insufficient power to climb steep slopes and continues to refuel Wait, when the motor is not rotating, the energizing current is the largest, in this case the temperature rises quickly. Some customers require that the softening breakdown of 200-class enameled wire should exceed 340℃, which is easy to achieve, and some require a temperature above 400℃, which can only be met by the paint model combination of certain specific manufacturers.
In the process of rapid heating of enameled wire, the paint film is impacted. Under the condition of higher than the temperature index, the cracking speed of the paint film polymer is higher than the crosslinking speed. The higher the temperature, the faster the cracking. Repeated blocking and heating, the paint film is insulated Ability will decline rapidly.
The bonding temperature of self-adhesive enameled wire is generally within 230°C, which is a one-time temperature rise and has almost no negative impact on insulation. The solvent remaining in the self-adhesive coating (helps bonding) will affect the stability of the insulating layer during long-term storage, and it is almost completely removed during the high-temperature bonding process, ensuring the safety of the insulation. There are also customers who use higher bonding temperatures, which requires evaluation of the action time and the endurance of the insulating layer.