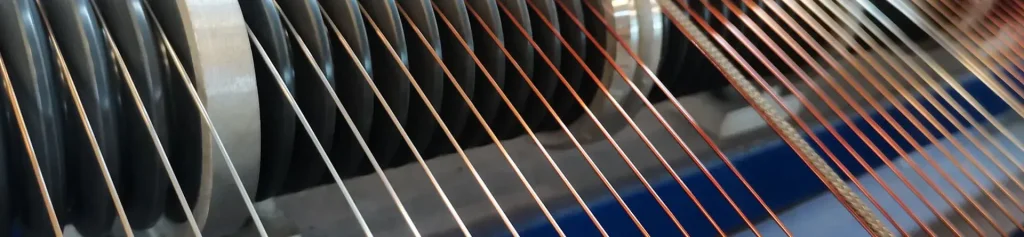
Transposed Wire Affect the Potential Transformer
Transposing wire (RTC) is a composite wires consisting of 5-80 enameled copper flat wires that are combined to allow wide faces to contact each other and are wrapped in a 0.08 to 0.12mm insulating shell made of paper or other fibrous material. The main categories are polyester rope, hardened type and self adhesive type products. It can be suitable for any working position in CTC cable, up to 120x26mm, can work stably in 240 degrees high temperature environment, and most of the transposition wire (RTC) is used in power transformers, electrical equipment, transmission and distribution centers, military and defense industries.
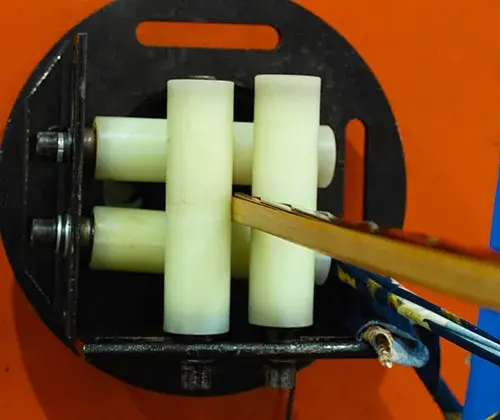
Transposition wire (RTC) is composed of lacquered copper wire, so it has higher working efficiency than single copper flat wire, and it can reduce the loss of power transmission. At the same time, due to the reduced size, transposition wire (RTC) can save more internal space for transformers and other power equipment, and improve the utilization rate of space. High electrical strength is also a feature of transposition wire (RTC) that can not be ignored. Enameled copper wire can conduct voltage above 2000KV, which can be increased to 3000-50000KV with paper insulation layer. Its thinner insulation provides better heat dissipation for wires, and thus better thermal stability, but it is better at resisting mechanical forces.
The Global Info Research survey shows the widespread use of transposed wires in the electrical industry especially in North America, Europe and main parts of Asia. Transposition wires (RTC) should be considered by manufacturers in the field of large power transformers. High quality transposition wire (RTC) is made by ZhengZhou LP Industry with American equipment. The interval of wires can be ensured to be 8mm during firing, and each copper wire is heated evenly. The film removal stage can ensure that the flame temperature is not higher than 700 degrees to avoid damaging the thermal conductivity of the material. The mature cooling process also enables the combustion oxides to be completely separated in the coolant. The welding and sanding process also involves multiple inspections, and the company ensures product quality that is worth for paying attention.