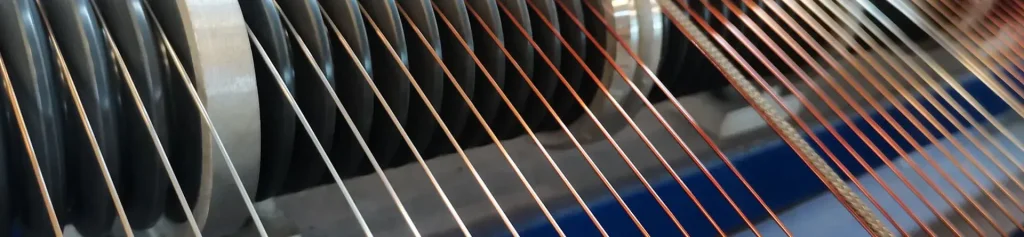
What Is Enamel Coating On Wire?
Chemically, enamel coating series consists of polyurethane, polyester, polyester imide, polyamide-imide. The solids content ranges from nearly 8% to 60% (1g/1h/180°C), and the viscosity ranges from 30 to 60,000 mPas (23°C). it is suitable for copper and aluminum wire with other conductive coils to better meet the needs of the work, enamel.coating varies greatly according to its use.
1. Polyurethane enamel provides excellent weldability of enameled wire up to 375°C and provides excellent cracking and pinhole resistance. These wire enamels are mainly used in small transformers, timers, relays, small motors, solenoids, clock coils, flyback transformers and magnetic heads.
2. Weldable polyester imide enamel coating is widely used for electromagnetic wires of relays, small transformers, mini motors, contactors, ignition coils, magnetic coils and automotive coils. It can be welded at temperatures higher than 450°C. These coatings are particularly suitable for small electric motors where windings are connected to collectors. The coated magnetic wire has good elasticity and dielectric and mechanical properties.
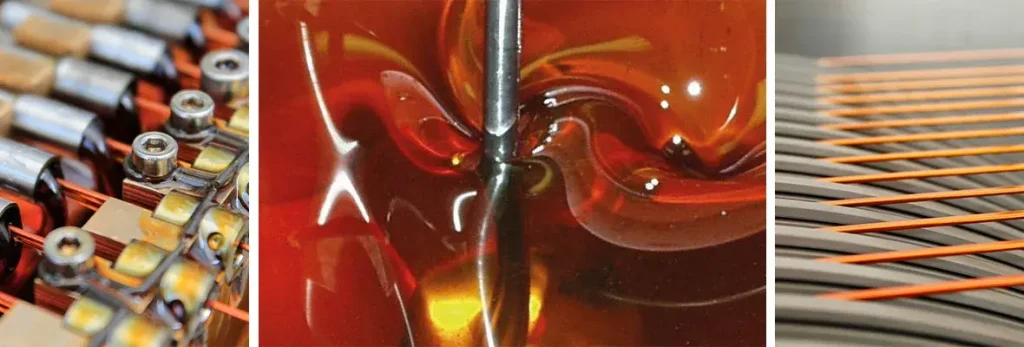
3. Modified polyester enamel coating is used as a primer for aluminum and copper wires, with excellent mechanical, electrical, chemical and heat resistance.
4. Polyester imide enamel coating has high heat resistance, excellent mechanical, electrical and chemical resistance. These enameled wire paints are widely used in electric motors, refrigeration equipment, transformer windings and fluorescent lamp ballasts. It has really good mechanical properties, high heat ratings and good chemical resistance, so it can be used to coat wires widely used in small transformers, cooling aggregates and electronic ballasts.
5. Polyamide-imide enamel coating can be used as a double or single coat, but both options offer excellent mechanical properties and chemical resistance. These products are specifically used to coat electrical wires in motors, refrigeration equipment, transformer windings and fluorescent lamp ballasts. For flat wire applications, large transformers and generators, it can be used as a flexible paint in combination with polyester or polyester imide primers to improve the mechanical, chemical and thermal properties of the paint. In some cases can also be used as a single coating on flat line applications.
6. Polyethylene-based nail enamel coating is suitable for heavy duty round and rectangular conductors. They have excellent mechanical stability, excellent adhesion to copper and tolerance to oil-immersed transformer. These highly complex enamels are mainly used in large generators and transformers due to their excellent mechanical properties. In addition to good dielectric properties, these enamels have excellent chemical resistance, which makes coated wires suitable for sealing applications and compliant with oil-immersed transformers. They are also ideal for the production of flat wires with transposed cable (CTCS).
7. Self-bonded enamel coating based on epoxy resin, polyvinyl butyal and polyamide is used to stabilize windings. They are mainly used to coat musical instrument coils, voice coils, speakers, small motors and sensors.