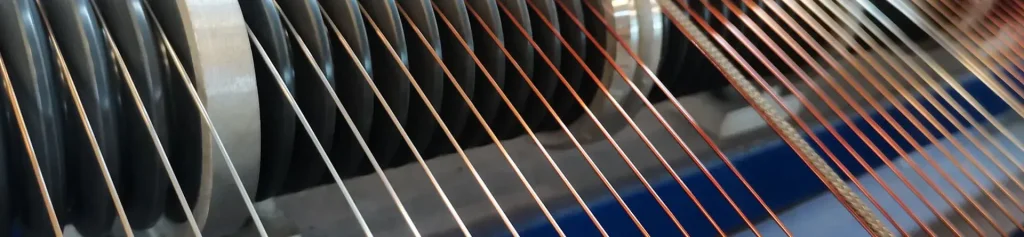
What Is The Performance Gap Between Copper And Aluminum Wires In Transformer Windings?
The different properties of wires in transformers are due to the differences in materials, that is the conductive characteristics of copper and aluminum. Specific performance in the following aspects:
First of all, the resistivity of copper is only about 60% of the aluminum as the conductor, in order to achieve the same loss and temperature rise, the employ of aluminum conductor cross-sectional area than copper conductor large more than 60%, so the same size and same parameter case, the size of aluminum is usually larger than copper for transformer, cooling area of transformer also increased at this time, therefore, the oil temperature rise is low;
The density of aluminum is only about 30% of copper, so aluminum is lighter than copper as conductor for distribution transformer;
Secondly, the melting point of the aluminum conductor is much lower than the copper conductor, so the temperature rise limit of the short-circuit current is 250℃, it is lower than the 350℃ of the copper conductor, so its design density is lower than the copper conductor, the cross-sectional area of the transformer wire is larger, so the volume is also larger than the copper conductor for transformer; The hardness of aluminum conductor is low, so the surface burrs are easy to eliminate, after the transformer is done, the probability of short circuit due to the burrs is reduced; Due to the low tensile and compressive strength of aluminum conductor and poor mechanical strength, the ability of aluminum conductor transformer to withstand short circuit is not as good as that of copper conductor transformer. In the calculation of stability, the stress of aluminum conductor should be less than 450kg/cm2, while the stress limit of copper conductor is 1600kg/cm2, and the bearing capacity is greatly improved.
Finally, the welding technology between aluminum and copper conductor is poor, and the quality of joint is not easy to guarantee, which affects the reliability of aluminum conductor to a certain extent. The specific heat of aluminum is 239% of that of copper as the conductor, but considering the difference in density and design density of both, the difference in actual thermal time constants between the both is not as obvious as the thermosteric anomaly, so the short-term overload capacity of dry type transformer made of aluminum conductor is not greatly affected.