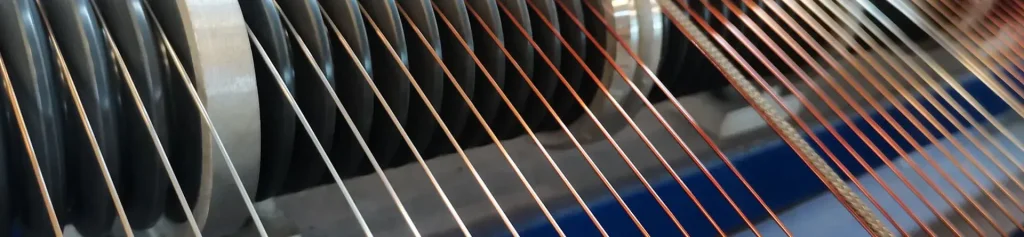
What’s The Difference Between Enameled Aluminum Wire And Enameled Copper Wire?
Perhaps you have some doubts about which enameled wire will solve your problem. The use of this type of wire for residential purposes has been widespread since about the mid-1960s. However, its popularity gradually declined from the late 1970s until it picked up again in the 1990s. Despite its high cost, copper is still used more widely than aluminum in conducting coils, but each material has its advantages and disadvantages.
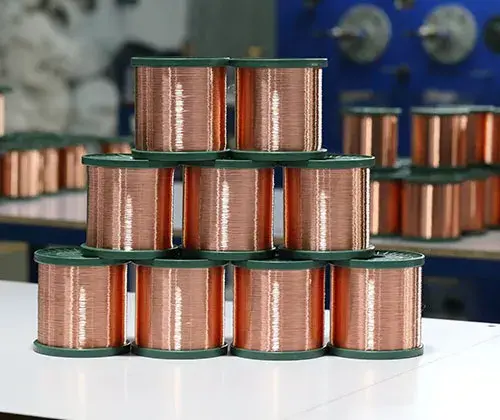
Copper is one of the highest electrical conductivity among metals, so it can be welded easily. It also makes it possible to use smaller conductors to transmit electrical loads. Smaller wires are easier to transport and install, and cost less, which helps manage wiring costs. Copper does not go through the same extreme expansion and contraction cycles as aluminum, so it is a more stable material. Copper can form very thin wires because of its high malleability, making it more versatile in a variety of working environments. Copper also has a high tensile strength, so it can withstand extreme stresses but shows minimal signs of wear. This makes wiring more durable than aluminum. Copper wiring also adds home value due to its strong elasticity, high durability, low maintenance and high performance. Aluminum, on the other hand, is very ductile and easy to use. The lightweight nature of aluminum is beneficial when wiring over long distances, and it is inexpensive, which makes the work less rigorous. Aluminum also reduces corona, a type of discharge associated with high power transmission. In terms of cost, aluminum is more affordable than copper wire. For aluminum, you will need about half the amount if switching to copper wire. When you need to do a lot of wiring in your home, the difference between the two materials can save a lot of money.
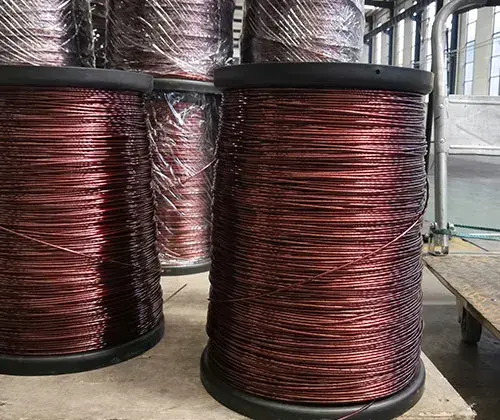
Copper wire costs much more than aluminum, so the overall cost can be prohibitive when a lot of wiring is required. Copper is also heavier, which makes wiring more difficult. More space is needed to hold the heavier wires in place, which also adds to the total cost. Copper requires a smaller cross section under a given current and is more expensive, and is easier to solder or otherwise join. Aluminum is less conductive and requires a larger cross section for a given current. Aluminum oxidizes quickly, preventing welding. In addition, depending on the particular alloy, aluminum tends to deform under pressure, loosening from improperly tightened screws, creating high resistance connections. Good connections require special consideration, especially for high-current applications. Aluminum wiring increases the risk of house fires if not properly installed. When the aluminum wire warms, it expands, and when it cools, it contracts. The tightness of the wiring decreases with each progressive temperature-cooling cycle, resulting in a phenomenon known as “cold creep”. These loose connections can cause sparks, which can lead to a fire. The wires gradually heat up and may even melt the surrounding insulation and fixtures, causing a fire. Aluminum wire requires higher maintenance than copper wire. This is partly due to high wear and tear rates and a greater risk of fire. For example, aluminum also experiences corrosion when it encounters certain metal compounds, and oxidation gives the connection greater resistance. This also increases maintenance costs.