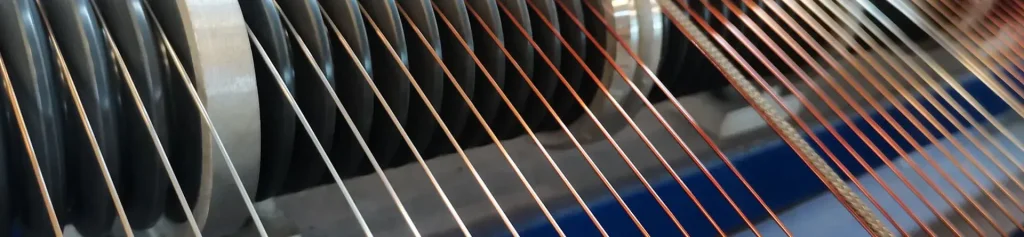
Winding Copper Wire For Use Up To 210°C 1/0.315mm Dia.
Copper wire is widely used in a variety of electrical and electronic applications due to its excellent electrical conductivity and mechanical properties. When it comes to winding copper wire for use up to 210°C, it is crucial to follow certain guidelines to ensure the wire’s longevity and performance.
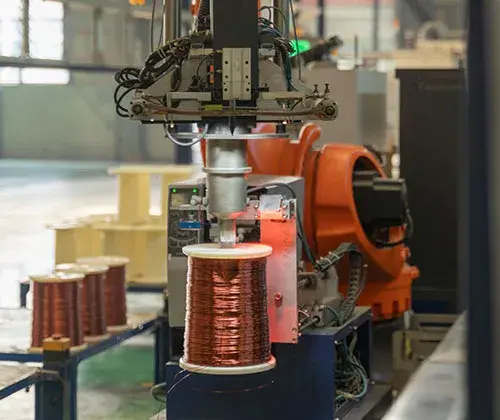
Firstly, it is important to select the appropriate wire gauge for the specific application. In this case, a 1/0.315mm diameter wire is being used, which is a relatively thin wire. It is essential to ensure that the wire can handle the current load it will be subjected to without overheating, which can cause the insulation to break down and lead to a short circuit.
Next, the winding process should be carried out with great care and attention to detail. The wire should be wound tightly and evenly, without any gaps or overlaps between turns. Any irregularities in the winding can cause the wire to generate excess heat, leading to insulation breakdown and eventual failure.
When winding copper wire for use up to 210°C, it is also important to choose the right type of insulation. The insulation should be able to withstand high temperatures without melting or breaking down, which can cause the wire to short circuit. It is recommended to use high-temperature-rated insulation, such as PTFE or silicone, which can withstand temperatures up to 260°C and 300°C, respectively.
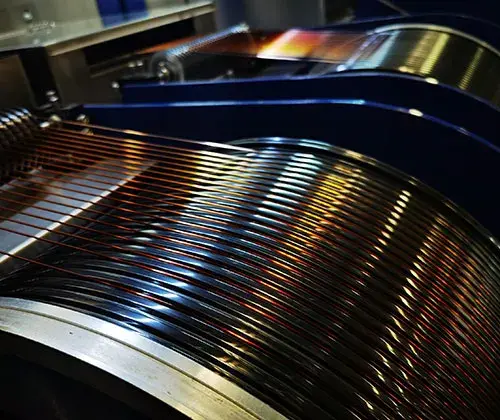
Furthermore, it is important to consider the environment in which the wire will be used. If the wire will be exposed to harsh conditions such as high humidity or corrosive chemicals, it is recommended to use insulation that is specifically designed to withstand these conditions.
Finally, it is important to test the wire for quality and performance after winding. This can include tests such as continuity testing and insulation resistance testing. These tests can help ensure that the wire has been wound correctly and is functioning properly.
In conclusion, winding copper wire for use up to 210°C requires careful attention to detail and adherence to certain guidelines. By choosing the appropriate wire gauge, using high-temperature-rated insulation, and carrying out the winding process with care, it is possible to create a high-quality, reliable wire that can withstand high temperatures and harsh environments.