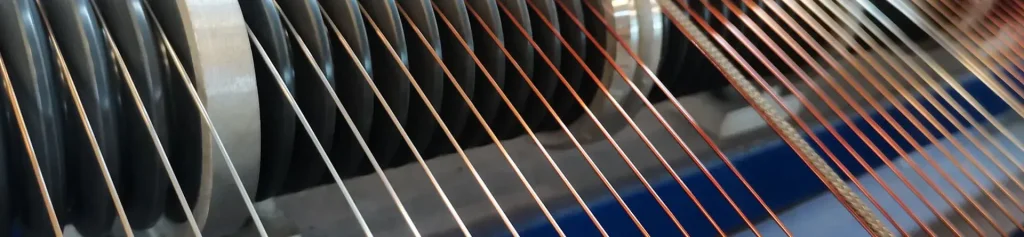
Annealing Processing of Enameled Wire: Strengthening the Foundation of Electrical Applications
Introduction:
In the world of electrical engineering, enameled wire plays a crucial role as a fundamental component for a wide range of applications. From motors and transformers to solenoids and inductors, enameled wire forms the backbone of these devices, carrying electrical current with precision and efficiency. One essential step in the production of enameled wire is the annealing process. In this blog, we will explore the significance of annealing and its impact on the properties and performance of enameled wire.

Understanding Enameled Wire:
Before delving into the annealing process, let’s first understand what enameled wire is. Enameled wire, also known as magnet wire, is a thin copper or aluminum wire coated with a layer of insulation material. This insulation, typically made of a polymer such as polyester, polyurethane, or polyimide, provides electrical insulation and protection to the wire.
The Importance of Annealing:
During the manufacturing process, enameled wire undergoes several stages, including wire drawing, cleaning, coating, and curing. However, one of the most critical steps is the annealing process. Annealing refers to the controlled heating and cooling of wire to alter its physical and electrical properties. This thermal treatment plays a pivotal role in enhancing the durability, flexibility, and conductivity of enameled wire.
Key Benefits of Annealing:
Stress Relief: The wire drawing process imparts residual stress and strain on the wire. Annealing helps alleviate this stress by heating the wire to a specific temperature, which allows for the redistribution of atomic forces within the wire. As a result, the wire becomes more relaxed and less prone to mechanical failure during subsequent processing or in service.
Improved Electrical Conductivity: Annealing increases the electrical conductivity of enameled wire by removing oxides, contaminants, and impurities that may have formed during earlier manufacturing stages. This leads to lower resistivity, reducing power loss and improving the overall efficiency of electrical devices.
Enhanced Mechanical Strength: Through annealing, the mechanical strength of enameled wire can be improved. The heat treatment allows for recrystallization and grain growth within the wire, resulting in a more uniform and robust microstructure. This enhanced structure increases the wire’s resistance to external stress, such as bending, twisting, or vibration, ensuring its longevity and reliability.
Flexibility and Formability: Annealing imparts greater flexibility to enameled wire, making it easier to handle during installation and allowing for tighter winding in coils and windings. The heat treatment softens the insulation coating, making it less brittle and more pliable. This flexibility is particularly advantageous for applications that require intricate and compact designs.