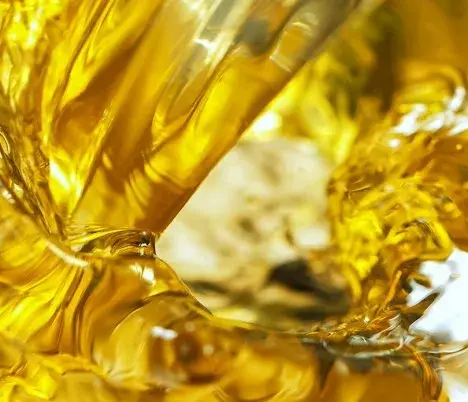
Introduction
Enameled wire is one of the most basic electrical materials as a winding wire, and has a large market space as a product supporting the electronics and electrical industry. Due to the friction between the enameled wire and mechanical equipment (guide wheel, mold, winding machine parts, etc.) into a tight, applicable coil.
In addition, since the enameled wire is wound from the original shaft to the wire package, it needs to go through 6 winding shafts and two times of felt wiping. The diameter of the enameled wire is sometimes as small as 0.03mm, so it is easy to be scratched if it is not protected. This causes the already thin wire to become locally thinner, which affects its strength and electrical conductivity.